Lean principles transformed material flows—so why are information flows still fragmented and inefficient?
Lean, automation, and AI have optimized production, but knowledge processes lag behind. They are onerous and expensive.
Since the middle of the last century, companies that make physical products have systematically identified and eliminated waste, streamlined workflows, and embraced continuous improvement. Mastering material flows has transformed shop floor efficiency from a visionary concept into a well-understood and achievable goal.
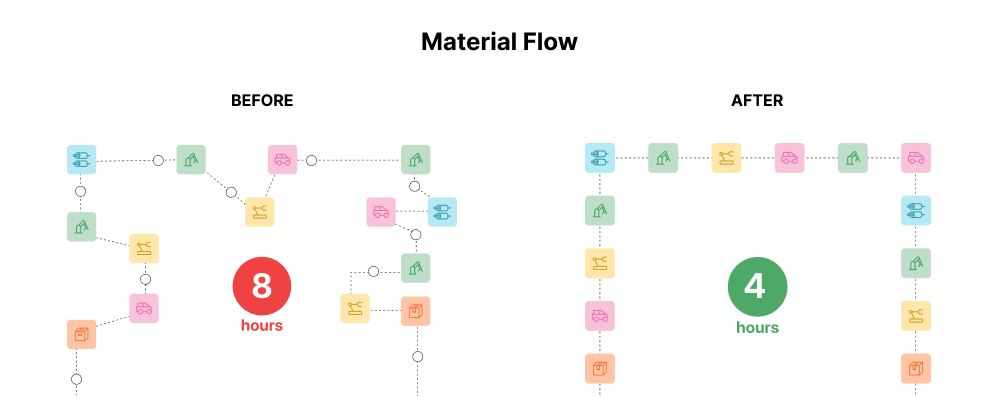
But problems persist with information flows beyond the shop floor. Instead of knowledge processes that have been studied, measured, and optimized, there’s often unclear ownership of tasks, lack of visibility across teams, and stalled hand-offs. You may see a burst of meetings, emails, and messages on a topic that could just as easily fall silent for weeks.
It’s not for a lack of trying. Companies that make physical products, like all companies, use a variety of systems for collaboration, project management, and knowledge sharing to drive alignment within and across teams.
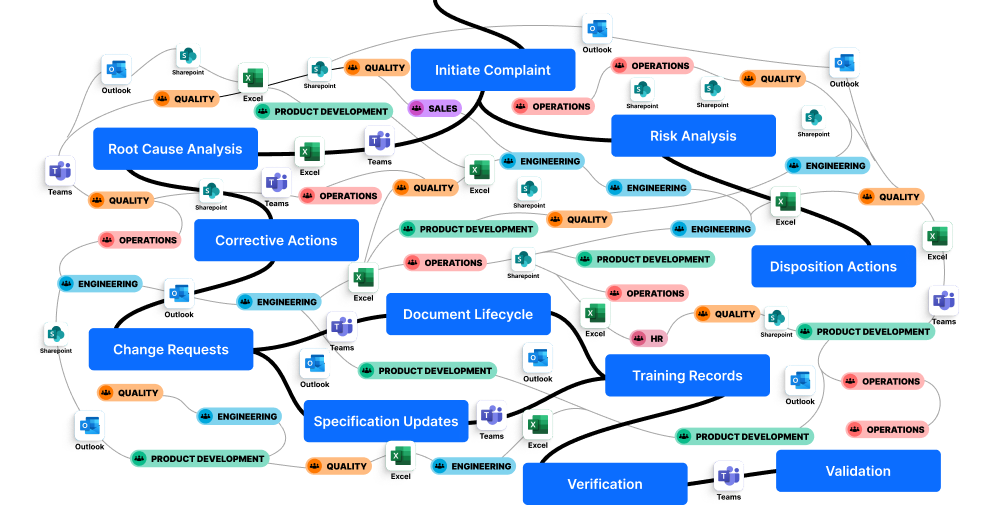
For FDA- and ISO-compliant companies, the added complexity of compliance processes means meetings are often the most efficient way to push these processes forward. Regardless, the timeline drags.
I’ve spent the last 20 years managing product development & manufacturing operations across the globe, including consumer goods in California, electronics in China, and industrial, medical, and food processing equipment in India. One of my co-founders led a food processing company as well as quality, R&D, and production teams for manufacturing and medical device companies.
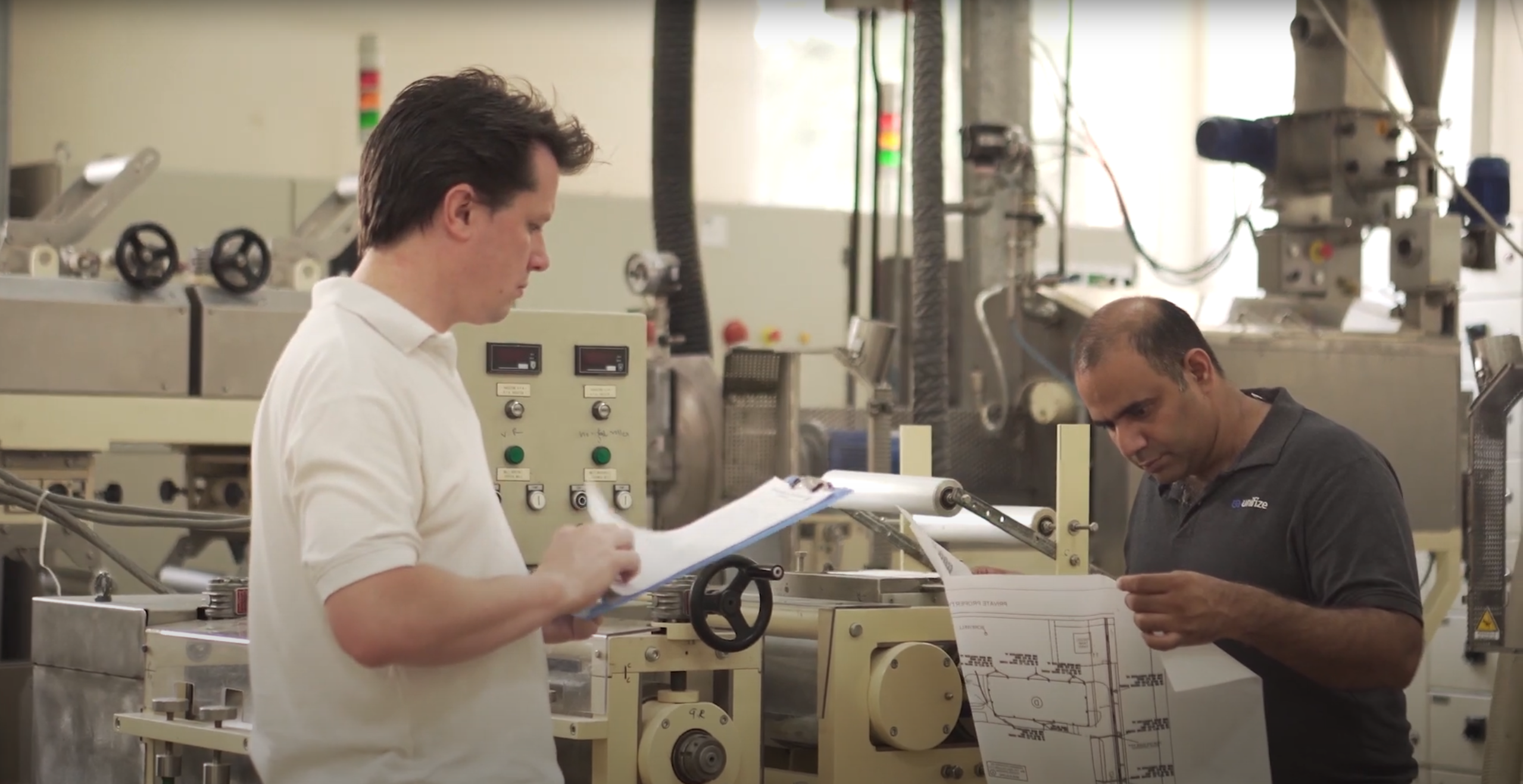
What we’ve found:
- While inefficiency is rampant in knowledge processes, no one seems able to quantify it or pinpoint its root causes. As a result, companies don’t prioritize finding real solutions.
- Since we can’t improve what we can’t measure, the impact is stalled productivity, delays and wasted resources. Somehow, we’ve come to accept this state of affairs as unavoidable.
The problem: siloed, scattered, and rigid knowledge processes
It’s ironic that process-driven organizations tolerate inefficiency in knowledge work that they would never tolerate on the production floor.
But if you still need to be convinced that there’s a problem, consider this: amidst the hype of the fourth industrial revolution, manufacturing productivity has actually declined since 2011.
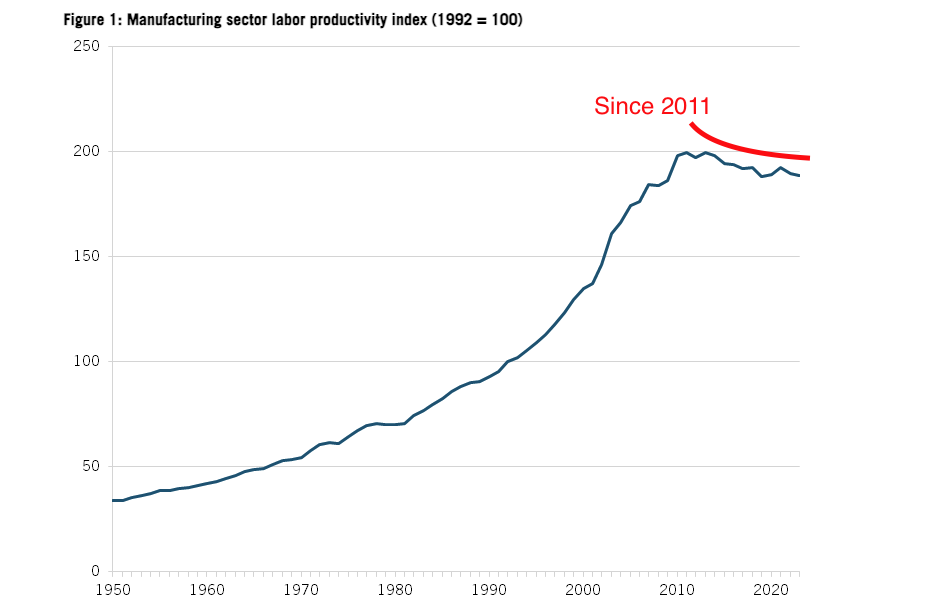
The problem of inefficient knowledge processes is structural, and we've been unable to see beyond the frame. The problem exists wherever knowledge work happens, but for those involved in compliance processes for physical products, it can be especially hard to function under the strain.
What’s happening here? For FDA/ISO companies, the legacy systems (QMS, PLM, MES) that dominate the industry are stuck in an outdated paradigm:
- Departmental silos separate teams and tools: While integrations and product suites have enabled some cross-functional collaboration by connecting workflows and data, most software is still designed as a point solution for a single team. These tools are optimized for individual workflows—not the full process lifecycle.
- Conversations happen outside the system: Communicating across different channels requires recreating context to bring different people into the loop and makes that context hard to find on demand. As a result, decisions, actions, and insights are often wrong, missing, or delayed
- Data and workflows are predetermined and overly structured: Existing systems lock teams into predefined, sequential workflows that resist adaptation. They require constant workarounds or costly, time-intensive, IT-supported customizations that can introduce errors and risk non-compliance.
If you take these issues together, it's no wonder these companies can’t measure knowledge processes or optimize them.
- First, neither teams nor management can see the processes end to end when they are scattered across email, messages, Sharepoint, project management apps, and point solutions.
- Second, the point solutions in question were never designed to be optimized in the first place. They are databases made for record-keeping, not continuous improvement.
AI won’t save you—fragmentation is the reason it hasn’t scaled
There’s a common belief that AI will transform knowledge processes:
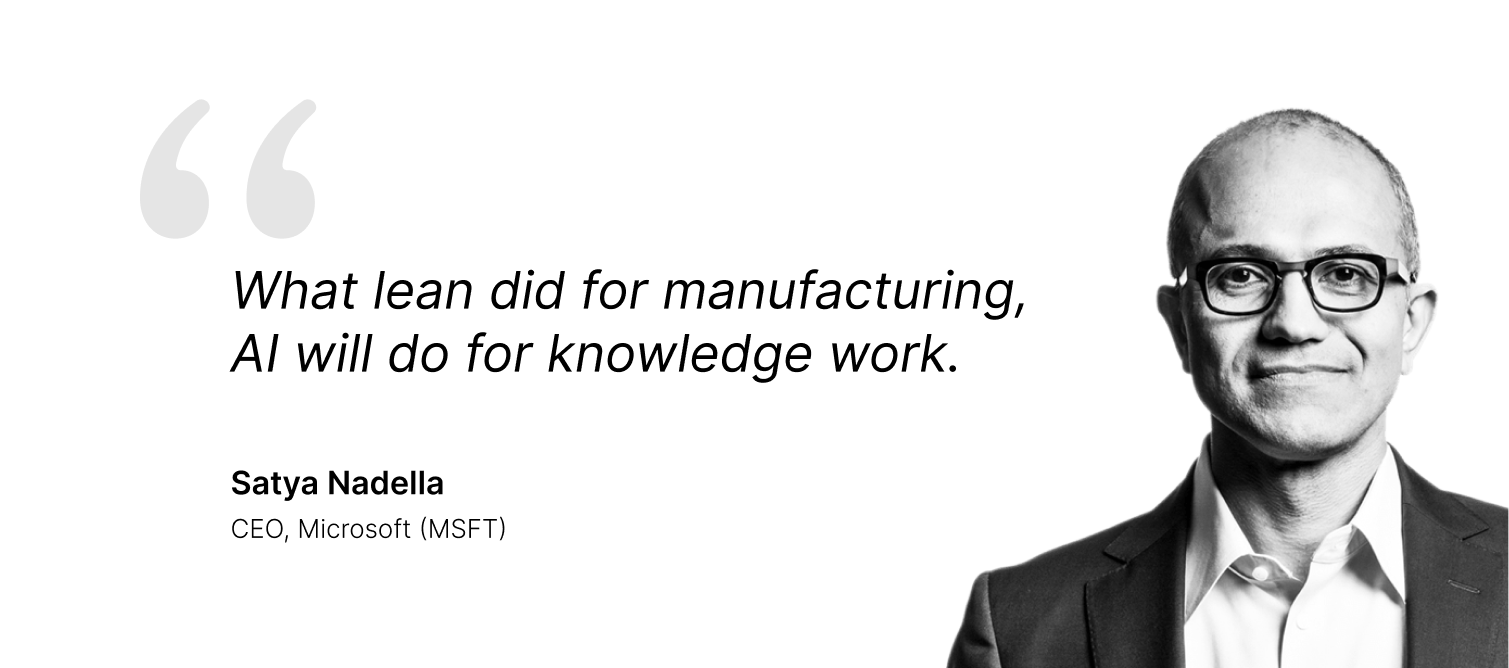
Traditional AI, like machine learning, process automation, and predictive analytics, has been used in business for years, especially for structured data like databases and spreadsheets. But these systems weren’t designed to handle unstructured knowledge work or adapt dynamically to real-world workflows.
Gen-AI takes this further by making sense of conversations, documents, and freeform content. We’ve all seen what gen AI can do at the individual level, and honestly, it’s amazing. But only 5% of businesses are using gen AI at scale. Without full process integration, gen AI, like traditional AI, struggles to scale in knowledge processes.
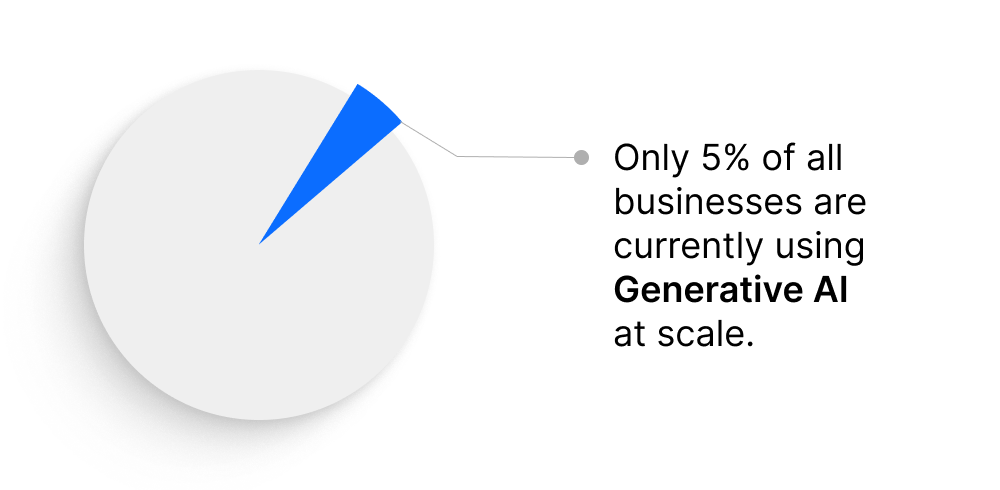
Pundits cite lack of training, leadership, or clear gen AI strategy as the biggest barriers to adoption. Those factors matter, but they overlook the real issue: gen AI is designed to be an individual productivity tool, not an enterprise-wide process optimizer.
To be effective in cross-functional workflows, AI needs what humans do: comprehensive, contextual, and reliable data. But most AI today is blind to the full process—it sees isolated tasks, not the entire process lifecycle. AI can only optimize knowledge processes when it has full visibility into workflows from end to end, including conversations, decisions, approvals, escalations, and compliance tracking as they unfold.
In most organizations today, AI doesn’t have that visibility—because workflows are scattered across disconnected systems.
When quality management has a QMS, engineering has a PLM, manufacturing has an MES and so on, neither people nor AI can connect the dots.
Further, when critical knowledge is scattered across emails, Slack, PDFs, and conversations, both people and AI lack the information necessary for intelligent, reliable analysis.
This is precisely why gen AI may be causing a revolution at the individual level, but few implementations have reached maturity business-wide. Some are even promoting the idea that feeding unstructured data to AI will be a new role for humans.
There has to be a better way.
Look beyond the frame: the fallacies built into existing software
Why do we have fragmentation and rigidity in software? Point solutions are easy to explain; software funding comes from individual department budgets, so vendors build for those silos. If we want different software, we have to give software makers different incentives.
The real issue runs deeper. The systems we use today weren’t designed for visibility, adaptability, or empowering humans—they were designed for control.
The assumptions behind them trace back to the Second Industrial Revolution (1870–1914), which brought us standardization on the production floor, but also ideas that have outlasted their usefulness: treating workers as interchangeable parts in a machine, centralizing decision-making, enforcing rigid hierarchies, and prioritizing short-term cost-cutting over long-term resilience.
These principles didn’t just shape factories—they became the default logic for business itself. As public companies optimized for quarterly earnings, they reinforced a bias toward rigid control, cost-cutting, and efficiency at the expense of adaptability, resilience, and long-term investment.
This thinking has been so pervasive that it has infiltrated software, processes, and organizational design, whereas with the stock market—it remains embedded today.
So while pundits and industry players repeatedly herald a new age of productivity and efficiency based on cross-functional teams, decentralized decision-making, and empowered employees, the expected gains are never fully realized.
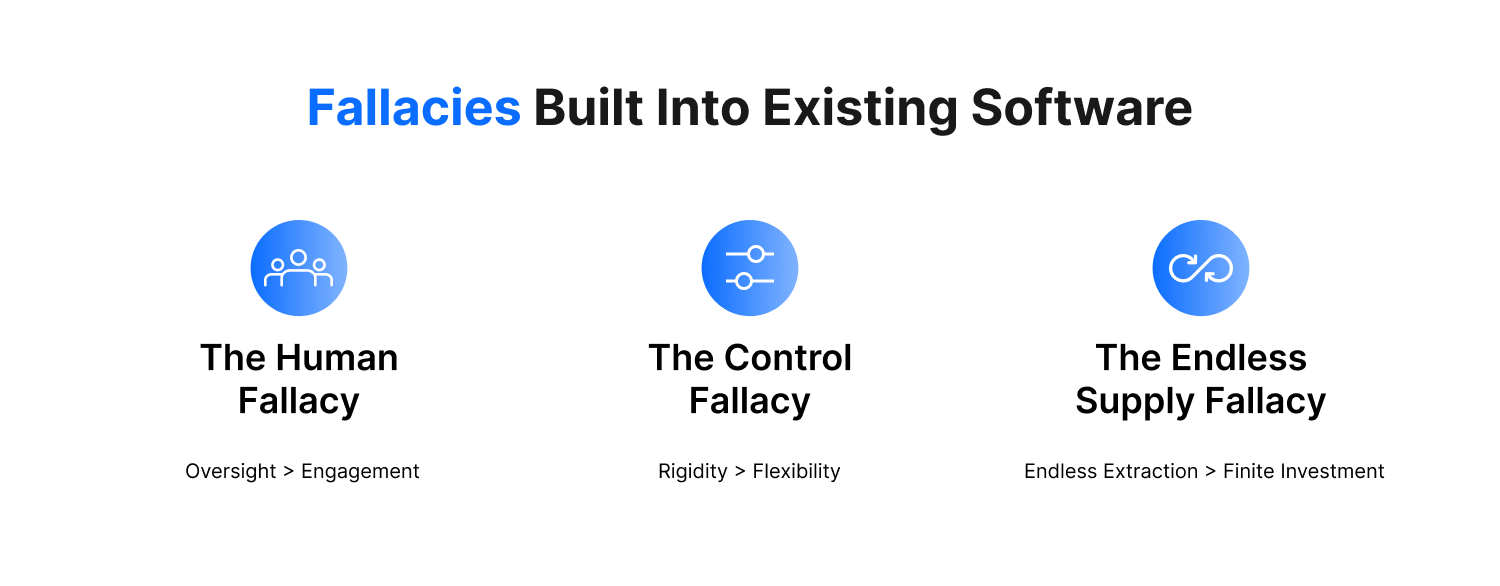
To move beyond this impasse, we need to expose three fallacies and return to first principles:
- The human fallacy: Humans are inefficient and error-prone, so we should replace them with technology and control decision-making from above.
- The impact: Existing systems are designed for oversight, not ease of use for people participating in workflows. These systems generate charts and reports, but dampen engagement with processes that are difficult to execute.
- First principle: Humans and technology are not competitors—when designed to collaborate, they amplify each other’s strengths. This is the foundation of collaborative intelligence, where AI and humans actively enhance each other’s capabilities. Humans are uniquely capable of understanding context, thinking critically, and solving problems creatively. AI, in turn, brings speed, scalability, and data-driven insights. When systems are thoughtfully built to support both, organizations unlock smarter decision-making, increased productivity, and more effective innovation.
- The control fallacy: The more control management has over people and processes, the more efficient the system becomes.
- The impact: Even as businesses embrace the idea of distributed decision-making, the fallacy of control still dominates software design in the form of structure. Structured databases, built for record keeping, support predetermined workflows. But when people can’t adapt a field or process to reality, it leads to more inefficiency, not less. These systems reduce engagement, force workarounds, slow decision-making, and make businesses less responsive to change.
- First principle: Empowerment, flexibility, and adaptability—not control—drive efficiency and resilience. When teams can optimize knowledge processes in real time as conditions shift—without IT intervention—they make better decisions, move faster, iterate without fear of failure, and continuously improve.
- The endless supply fallacy: There is an endless supply of resources, including people.
- The impact: In a world of endless supply, businesses have the luxury of extraction: maximizing short-term profits and cutting costs without considering long-term investment. This fallacy still shapes market expectations today, where success is measured by immediate returns rather than sustainable growth. Salaried knowledge workers result from this mindset—and reinforce it. Because businesses don’t feel the immediate cost of inefficiency in knowledge processes, they tolerate waste that they would never accept in production. Like businesses, software assumes workers can push harder, compensate for inefficiencies, or simply be replaced if they burn out. The result is systems that treat human energy as an unlimited resource, wasting time, attention, and effort.
- First principle: People, materials, finances, and strategic priorities are all finite. To make the most of them, businesses need a constant practice of empowering their teams, identifying inefficiencies, and streamlining processes—even in their software.
For more than a century, companies have pursued efficiency and productivity by making the needs of the people in the system secondary. This approach is also embedded in Industry 4.0, which prioritizes advanced technology as the primary driver of efficiency and productivity. Perhaps this is why many companies have found it lacking as a framework for true industrial transformation, and productivity gains have not shown up.
We believe the vision of Industry 5.0 is more useful. It builds on the use of advanced technologies to drive productivity and efficiency, but it challenges the outdated industrial mindset that has shaped work for the last 100 years.
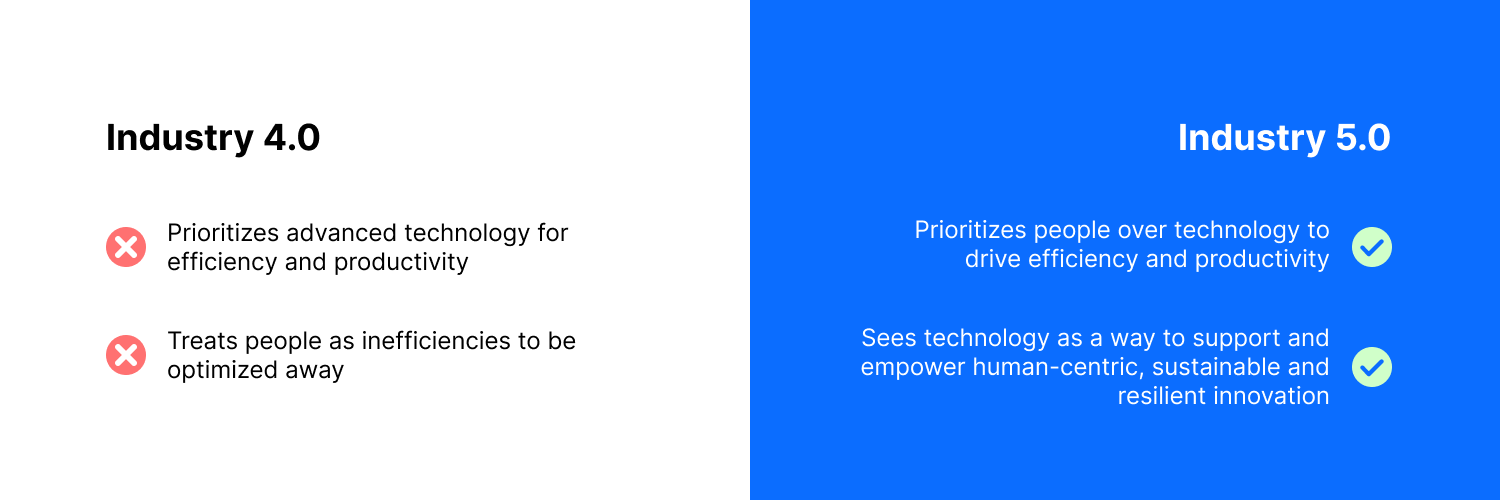
Instead of treating people as inefficiencies to be optimized away, resources to be extracted, or cogs in a rigid system, Industry 5.0 puts humans at the center. It sees technology as a way to support and empower humans. It envisions a future where businesses enhance human capabilities rather than replace them—where industry contributes to society through human-centric, resilient, and sustainable innovation.
A new paradigm: a unified, adaptable system for collaborative intelligence
Industry 5.0 isn’t just an aspiration—it’s a practical framework for driving better business outcomes. It recognizes that true operational excellence comes from systems that are designed to amplify human capacity, adapt to changing conditions, and make the best use of finite resources.
Industry 5.0 helps us see beyond the outdated notions from earlier industrial eras, and it’s the guiding framework for how we design Unifize:
- Using human-centric, resilient, and sustainable innovation as the frame, we’ve reimagined how FDA- and ISO-compliant industries design, refine, and collaborate on knowledge processes.
- Instead of forcing people and AI to fight against fragmented, rigid systems, Unifize creates an intelligent, adaptable, and collaborative platform where both can thrive.
- The outcome is collaborative intelligence. Organizations achieve the greatest performance gains when AI and humans work together, not when they compete. Instead of replacing human expertise, AI enhances speed, scalability, and insight, while humans drive creativity, leadership, and decision-making.
Our approach optimizes knowledge processes across the entire lifecycle, with a focus on quality, operations, and product development teams. We help them work faster, smarter, and more collaboratively to innovate their products and processes.
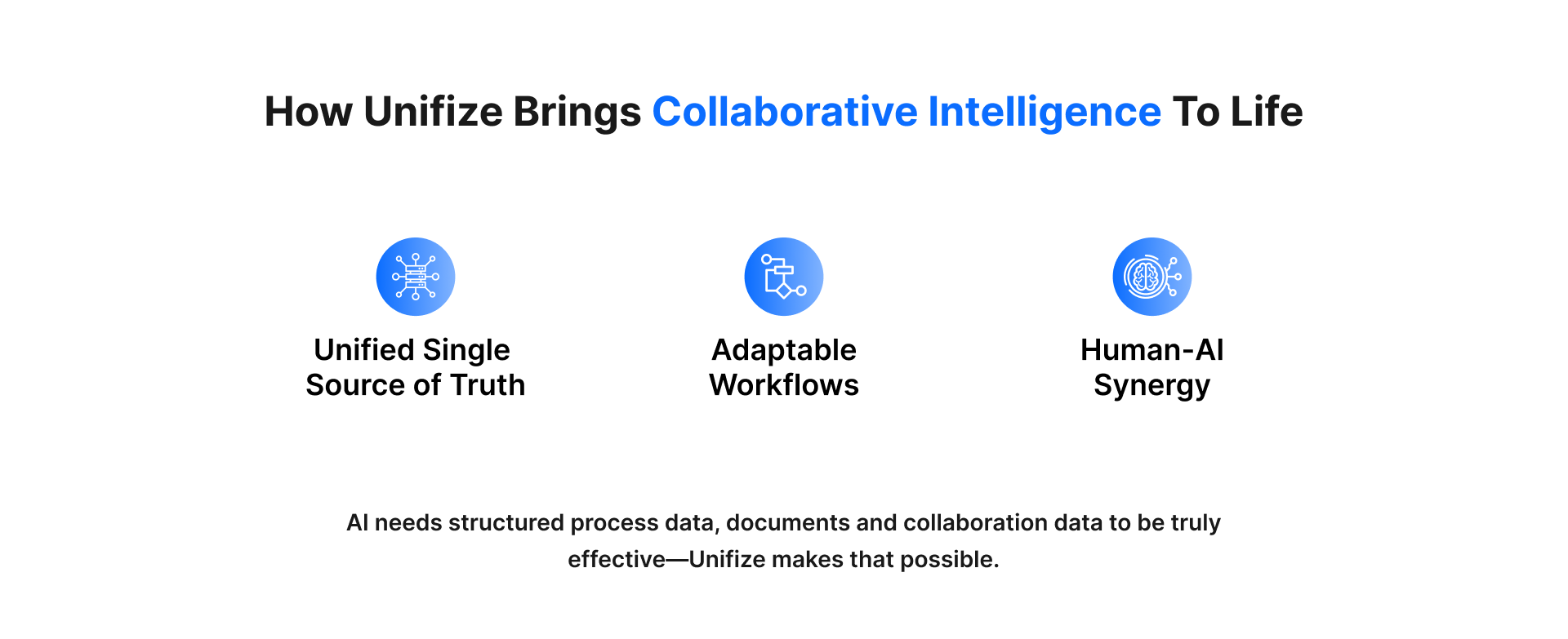
Here’s how Unifize makes this a reality:
- Unify people, processes, and information into a single source of truth
- Streamline collaboration by embedding real-time conversations, updates, and approvals directly into workflows, eliminating delays caused by email, messaging, meetings, and calls.
- Ensure shared visibility and accountability by centralizing workflows and data across the entire process lifecycle, including communication from suppliers and customers.
- Build in adaptability and ease of use
- Empower teams with no-code, drag-and-drop tools that make it easy to implement, adjust, and optimize workflows without IT intervention.
- Increase productivity and the focus on higher-order tasks by automating action logging, dynamically linking related data points, and automatically tracking ownership, approvals, escalations, and process changes, ensuring traceability and a comprehensive, unalterable audit trail.
- Harness AI to augment human effectiveness and optimize processes
- Work with any AI model, whether structured or unstructured, custom or generic, language-based or data-driven. Unifize's flexible AI architecture can leverage process metadata (e.g., code), quantitative insights (e.g., measurements, timestamps, financials), and contextual understanding (e.g., conversations and documents).
- Embed AI into real workflows, not just data. AI is integrated across the full process lifecycle, not just for a single person or team, ensuring real-time insights flow directly into actions, conversations, and decision-making. AI highlights inefficiencies, recommends optimizations, and ensures compliance is built into every process.
- Track AI’s role in decision-making. Every AI-driven recommendation is transparent, auditable, and tied to real business outcomes.
The tangible impact of Unifize:
- Measure and reduce cycle times. When everything is in one place, teams can track process timelines, identify bottlenecks, and drive accountability.
- Faster workflow adoption & process alignment. Teams collaborate more effectively even as business needs change.
- Clear accountability & reduced delays. Ownership is always visible, ensuring timely action and continuous progress.
- AI-driven process optimization. AI transforms workflows into self-optimizing systems, enabling faster decisions, fewer errors, and more proactive management.
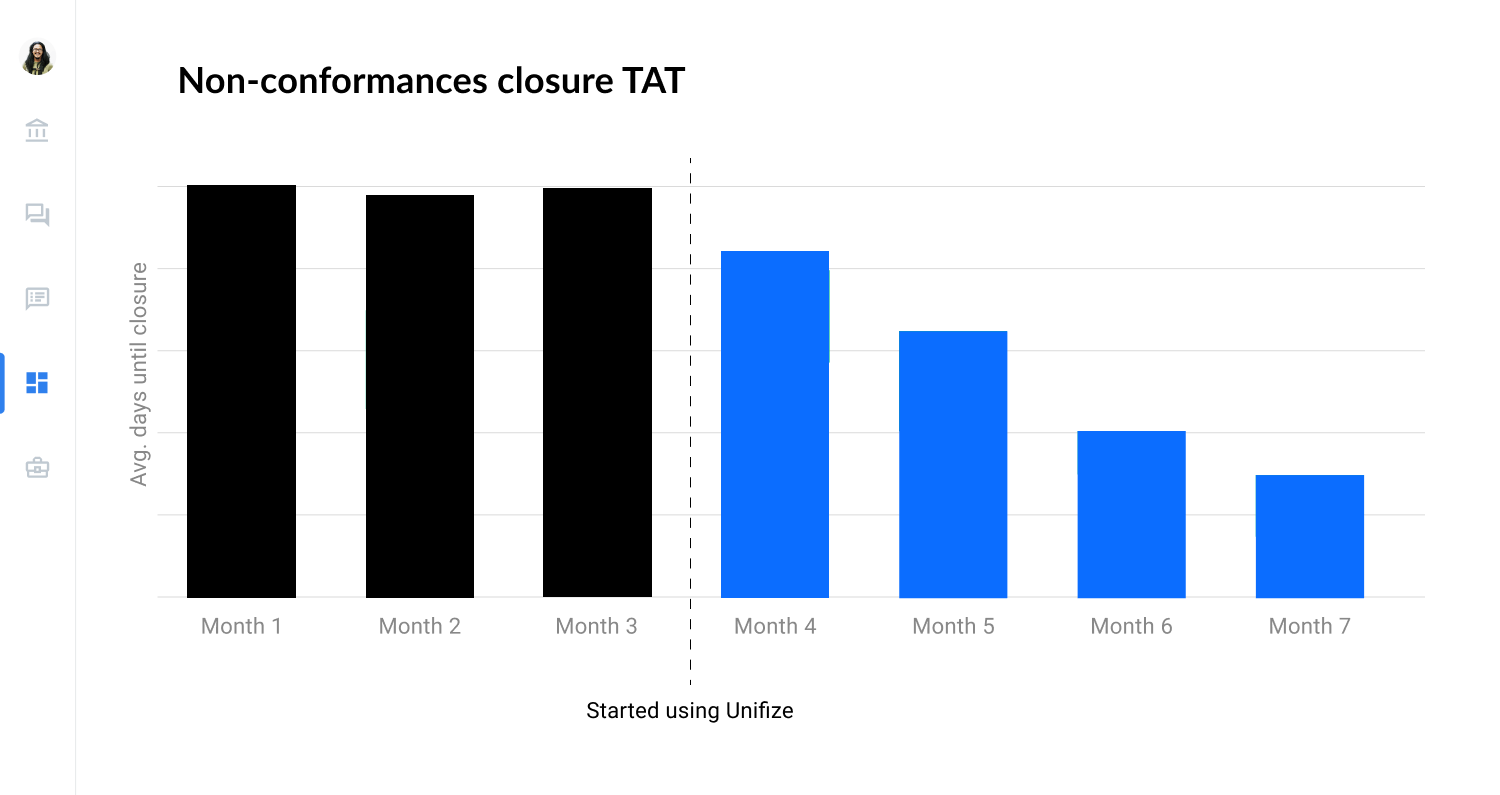
By enabling this level of visibility and efficiency, Unifize helps teams not just improve execution but also manage risk and compliance, drive operational efficiency, and accelerate innovation.
Conclusion: Unlocking the Full Potential of People and Technology
For decades, businesses have optimized production, yet knowledge processes remain fragmented, inefficient, and rigid. AI alone hasn’t solved this problem because it’s been held back by fragmented data.
Unifize changes that.
It uses Industry 5.0 principles to rethink how we design software. It enables collaborative intelligence by embedding AI and human collaboration directly into knowledge workflows, Unifize creates an intelligent, adaptable system where people and AI work together in real time.
We can finally realize the promise of cross-functional teams and distributed decision making. We can make knowledge processes the next frontier for innovation.
With a unified system that is flexible, transparent, and built for continuous improvement, businesses can finally bring the same level of efficiency, agility, and innovation to knowledge work that they’ve achieved in production.
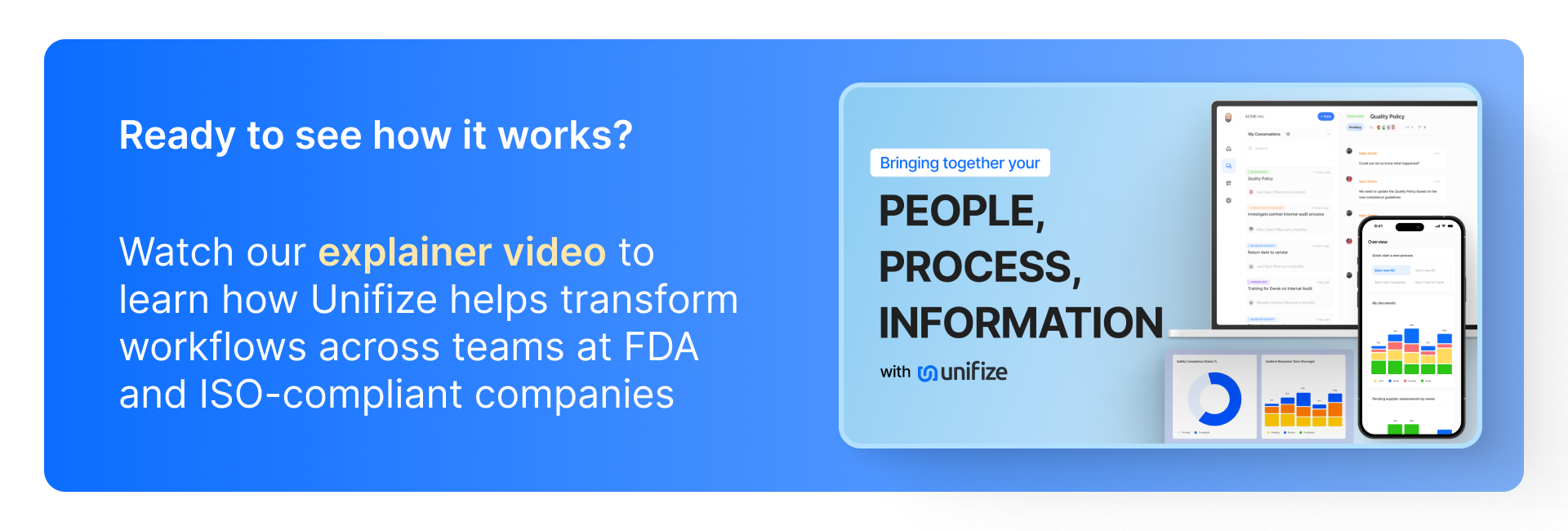
-