About Biovation Labs
Biovation Labs is the manufacturing arm of Adaptive Health, a consumer health company based in North Carolina that supplies nutraceuticals and dietary supplements to companies like Walgreens, GEC, CVS and Target. Biovation products are also sold directly to consumers under the Healthy Directions brand name.Biovation has approximately 125 employees in a facility in Salt Lake City, Utah. They are regulated by the FDA and follow GMP under 21 CFR Part 111 as well as 21 CFR Part 11 for their electronic systems. They were also an early adopter of NSA 455-2 standard for dietary supplements, which is part of the Global Retailers &Manufacturing alliance.
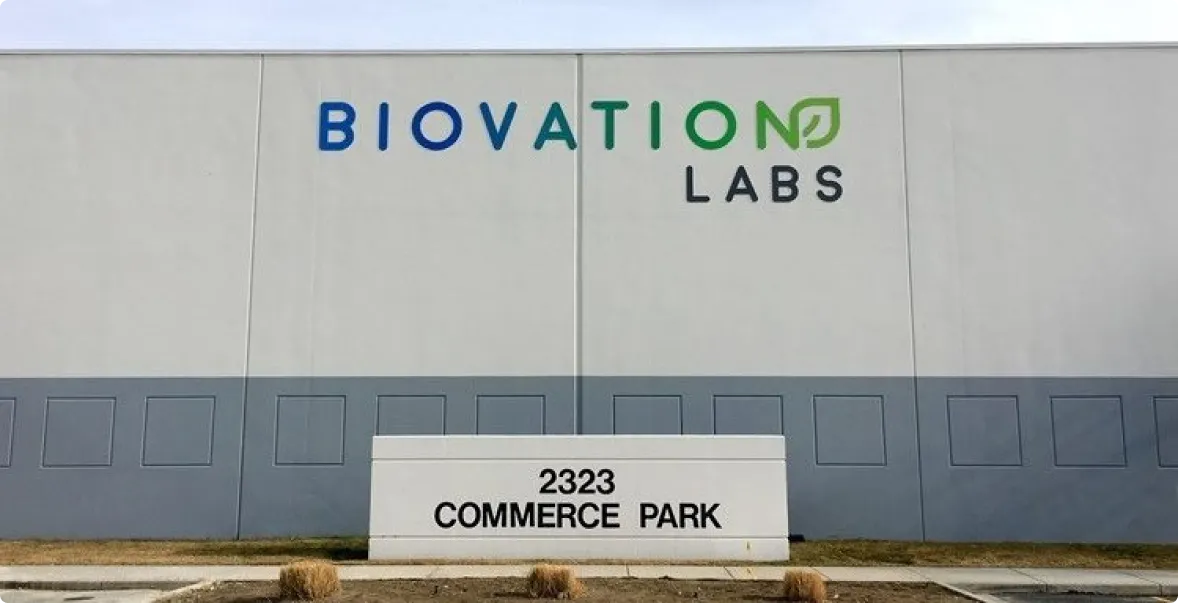
About Jesse Kolstad
Jesse Kolstad is Biovation Labs’ Director of Quality and Compliance. He holds a degree in Biochemistry, an MBA in technology management, and spent much of his career at a CRO for the pharmaceutical industry. He has spent more than 10 years working with eQMS systems at various different companies, including MasterControl, JD Edwards and Ross.His experience with these systems in previous companies led him to seek out a less rigid and more flexible alternative at Bi.
“Systems like MasterControl, JD Edwards and Ross ultimately became like $10m dollar paperweights, which just added steps to what people are already doing offline anyway…these systems are usually built and implemented by managers, and the user interface is always overlooked, which makes adoption hard.”
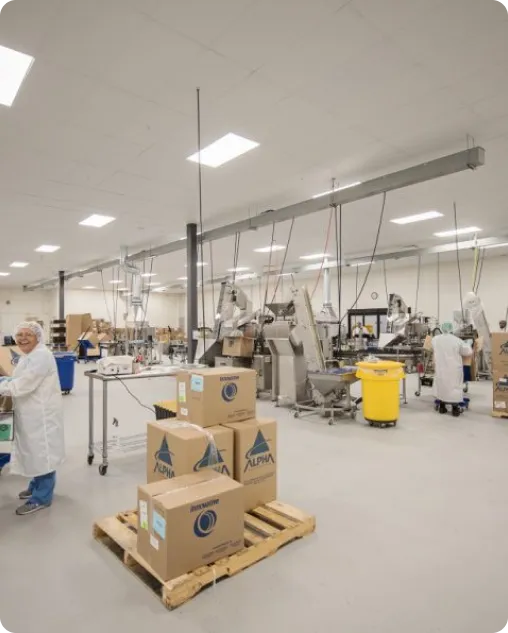
Problems with MasterControl
Biovation Labs had already implemented MasterControl and had been using the system for more than a year before Jesse joined the company. However, Jesse felt that the benefits of implementing a flexible, user-first, cost-effective system far outweighed the time and effort involved in transitioning systems.
The following is a summary of the problems they faced with MasterControl:
- Inflexibility of the system to customizations and process changes.
- Lack of collaboration across different internal and external teams.
- Low engagement with quality processes from other departments.
- Very high costs and lack of responsive support.
- A lot of wasted time trying to tie different systems together.
- A user interface that was primarily about structure and control, not usability.
Ultimately, these problems meant that Biovation would find it difficult and/or expensive to meet its compliance and continuous improvement objectives if it continued to use MasterControl.
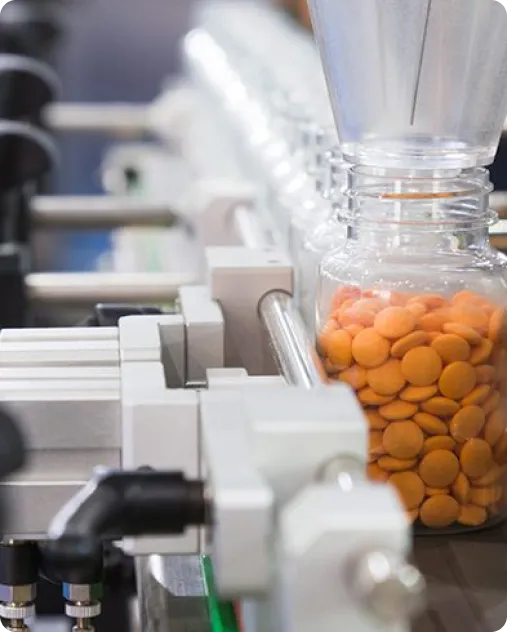
What made Biovation choose Unifize
Jesse combined his previous experience of eQMS systems along with a fresh search of the best available QMS systems at the time. He ultimately shortlisted Unifize and Cloudtheapp and selected Unifize for the following reasons:
- The simple, easy-to-use, conversational interface meant that his team was able to pick up how it worked almost instantly and drive accountability across different collaborating teams.
- Unifize was quickly able to map to his processes rather than forcing him to change his system to fit a new software.
- Unifize used printable QR codes to enable real-time lot traceability.
- Unifize’s pricing model was completely transparent and eliminated his risk until after it was proven to work.
- Unifize was cloud-based, meaning Jesse and his team could manage the implementation entirely on their own without the need for involvement from their overloaded IT team.
- Unifize offered support throughout the onboarding process, and would help him make any changes he required on an as-needed basis at no extra cost.
- Unifize took up the burden of migrating the existing data from MasterControl.
.png)
How does Biovation use Unifize
Biovation Labs went live with Unifize across the organization in February 2021 to manage the following processes:
- NCs/disposal actions
- CAPAs
- Complaints
- Document management
- Product specifications
- Raw material specifications
- Packaging specifications
- Finished good specifications
Over the next 3-6 months, Biovation had expanded their use of Unifize to cover the following additional processes:
- New supplier requests
- Lot traceability (including printable QR codes)
- Artwork approvals
- Change requests
- Ingredient and ingredient approvals
- Internal audits
- Supplier management
- Supplier onboarding/audits
- Training and training records
- Out of specs
What were the results?
The results were almost instantaneous. By using Unifize, Biovation Labs was able to:
- Reduce external testing costs by more than 50%.
- Reduced key processes like artwork approvals, CAPAs and resolving OOS from months to hours.
- Improve collaboration and engagement with different departments and suppliers on quality processes, especially around inwarding raw materials and lot releases.
- Increased confidence from their ability to get real-time, cradle-to-grave connectivity and visibility in their quality processes.
- Increase visibility into 6 core quality processes by bringing everything into 1 place.
- Meet their compliance requirements under 21 CFR Part 111 and 21 CFR Part 11.
“Unifize afforded us the ability to collaborate, collect and interpret data more effectively, so that immediately I could drive down our testing costs from $146k in February to $65k in two months. The more we use it, the lower that number goes.”
- Jesse Kolstad