Unifize Results
Speed to compliance
Faster time-to-market
Fewer meetings
But what we've known from what I experience was, is we were able to get there with the system. We still there with the system. The system has what is needed to provide us what we're looking for, because every company, admittedly, is trying to get compliant. If we educate people, if we get people the education that they need and to get over the fear factor, I think 90% of those things can be resolved because most people will go to what they're most familiar with.What I worked with from a different company, but they're not willing to sit down and look at what the demographics are saying. People are into social media now. People are moving fast into fast paced world. But technologies are still antiquated. So there's a disconnect here, right? So while we're moving at a fast pace at home with dragging at work, so why can't we continue that speed while we at work?If your supplier has issues and you're not informed on time, you want to have an alternate supplier in place. If your suppliers are not qualified, you may not know that that needs to happen. And so when you have an integrated system that speaks to itself and is giving you all this data, you literally have the pulse of the organization in your hands as an executive at a money bound access.
Related Case Study Videos
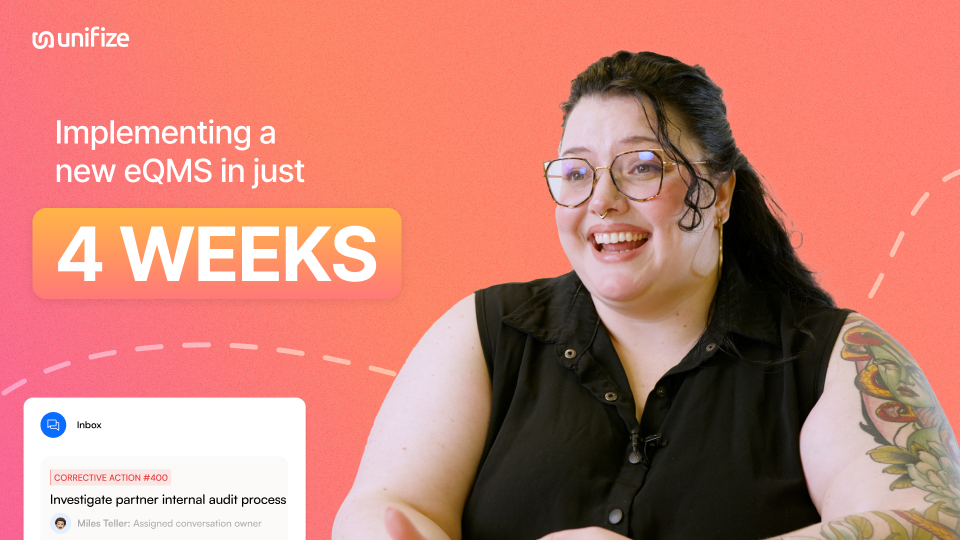

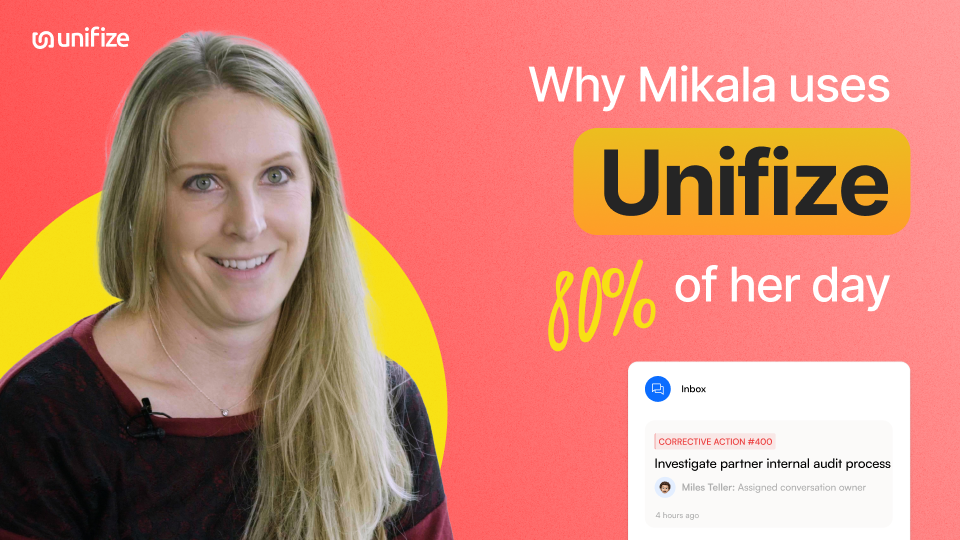

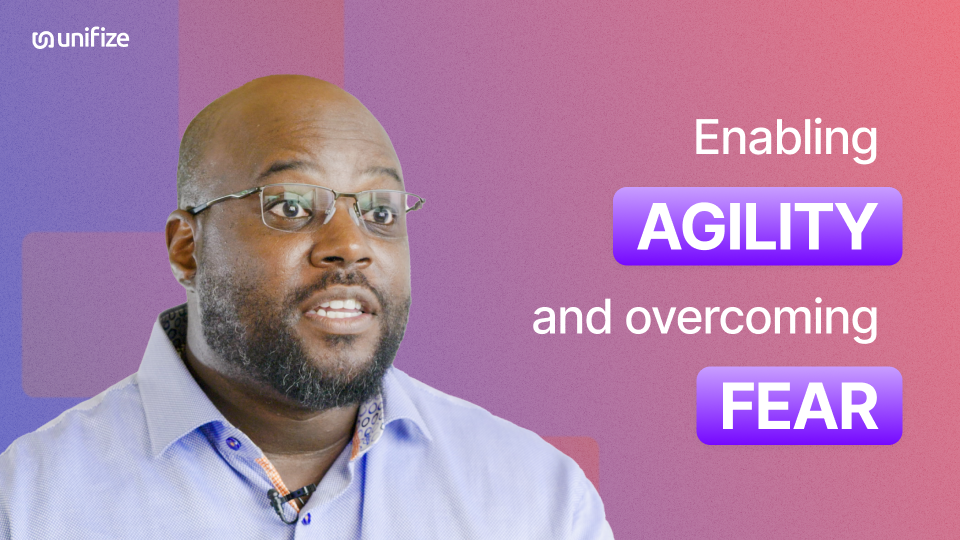

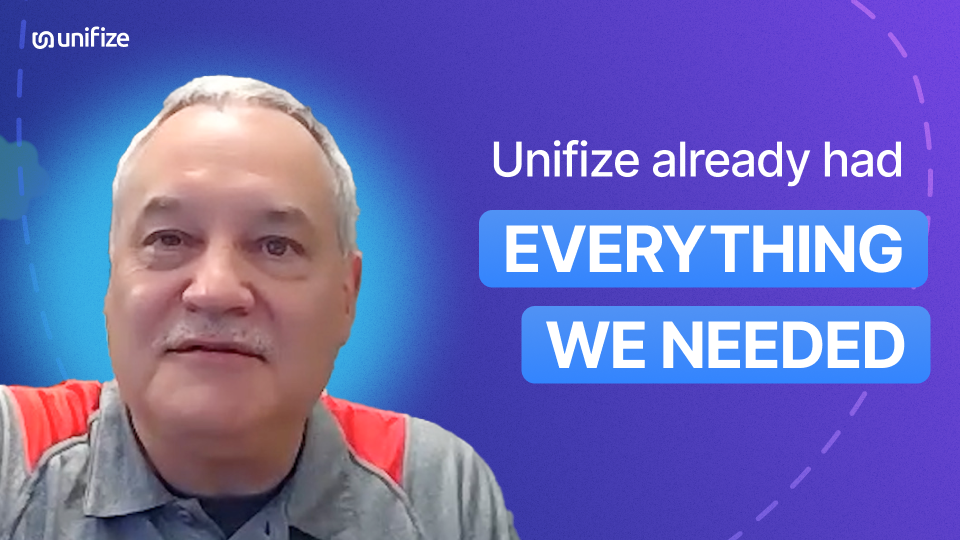

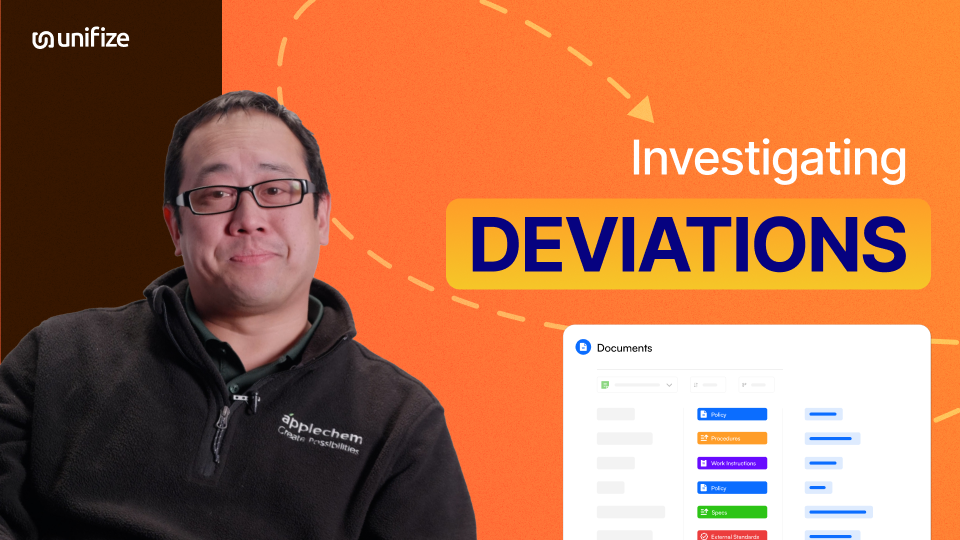

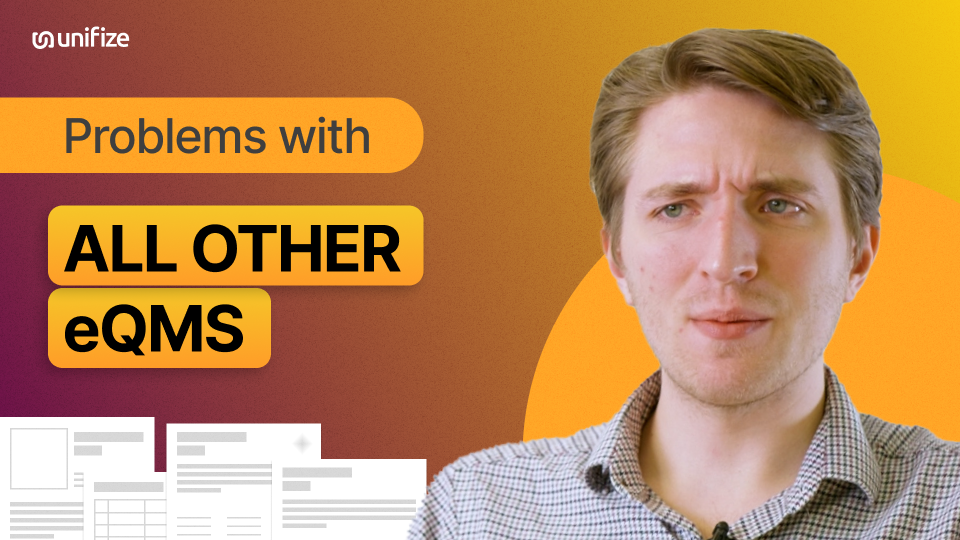

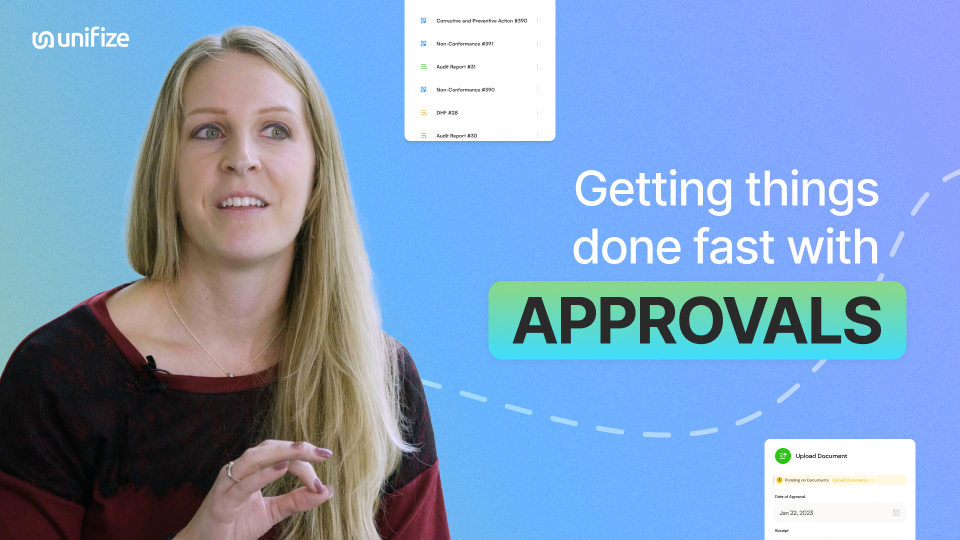

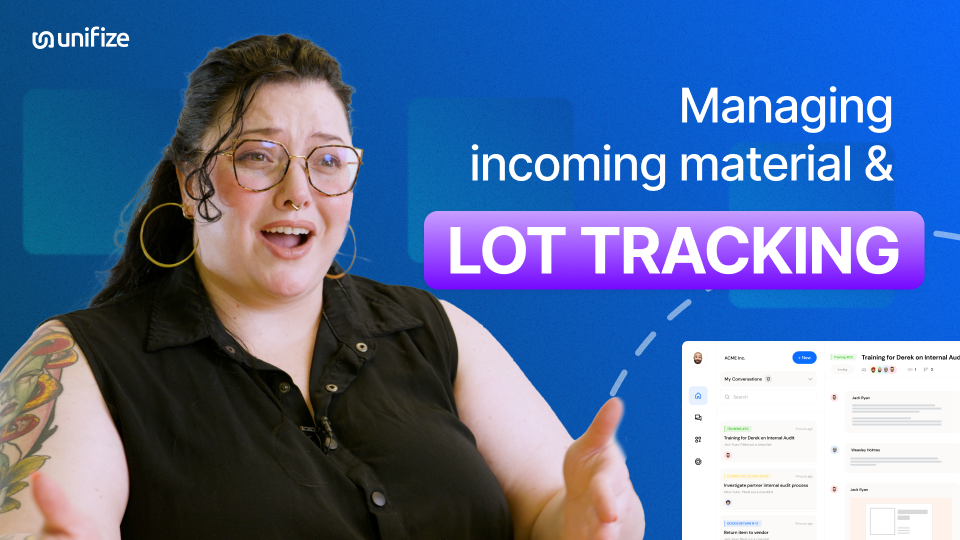

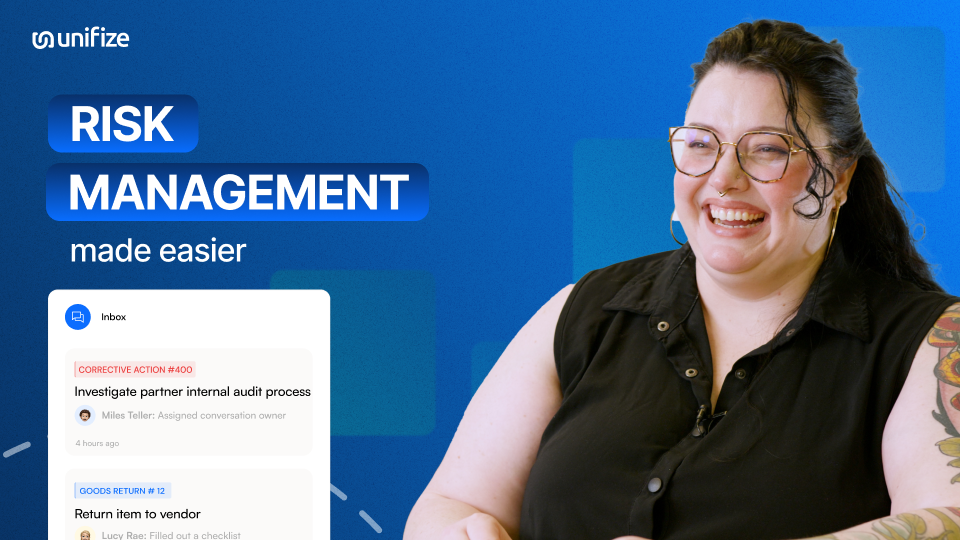

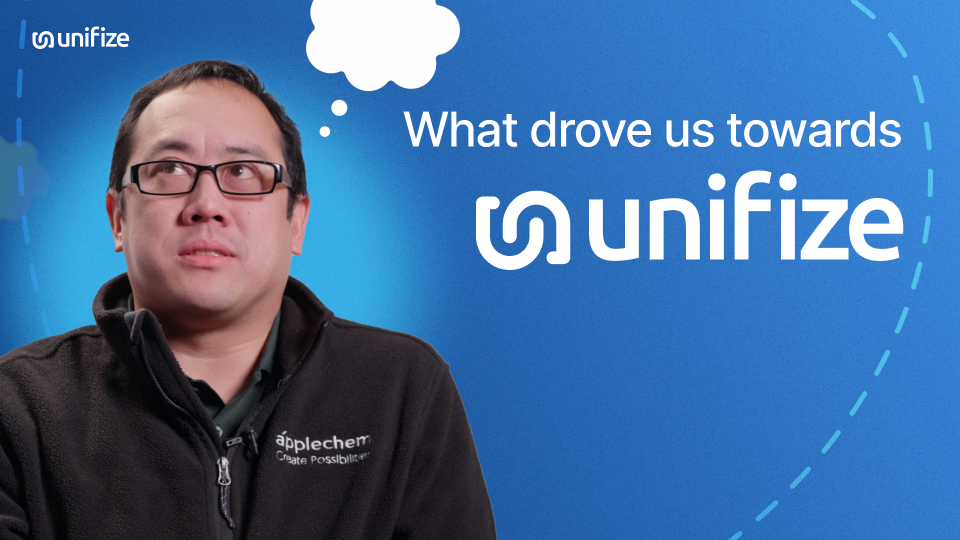

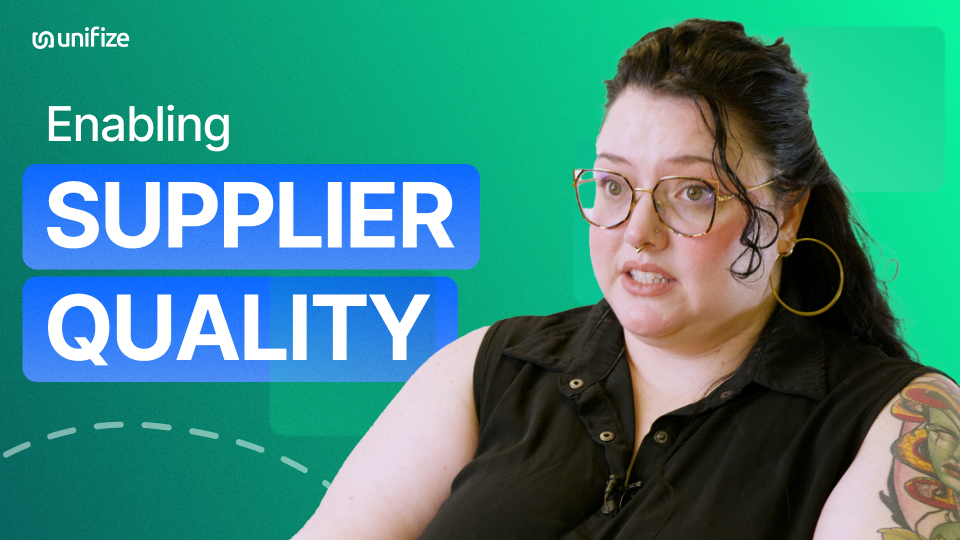

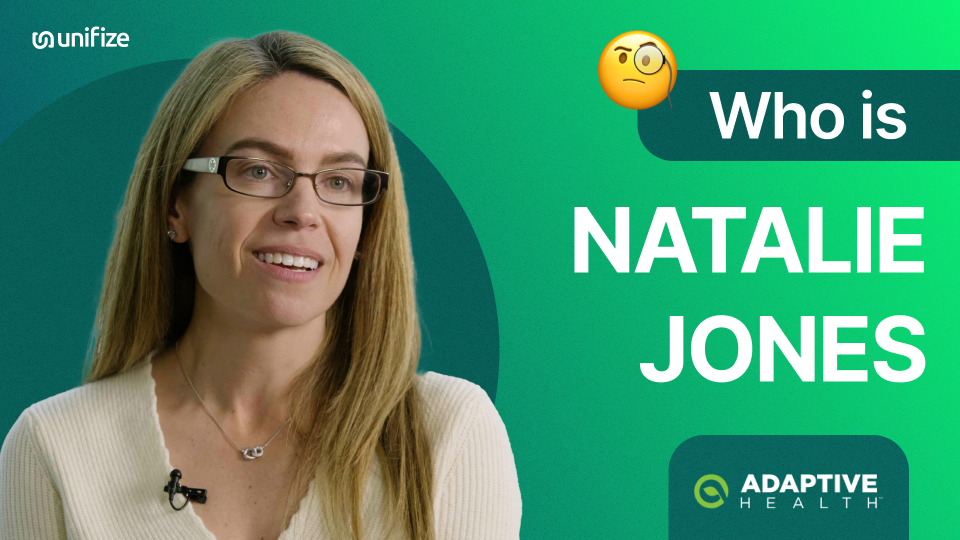

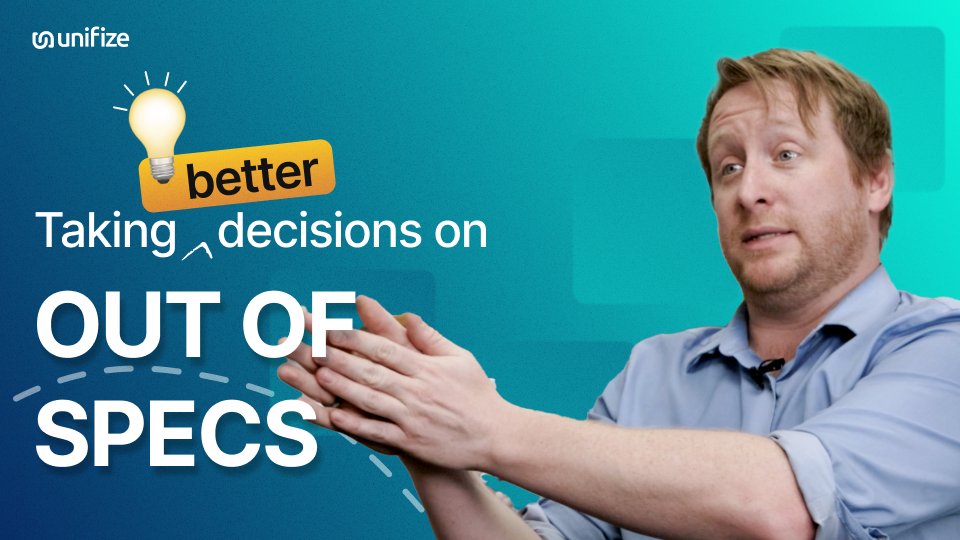

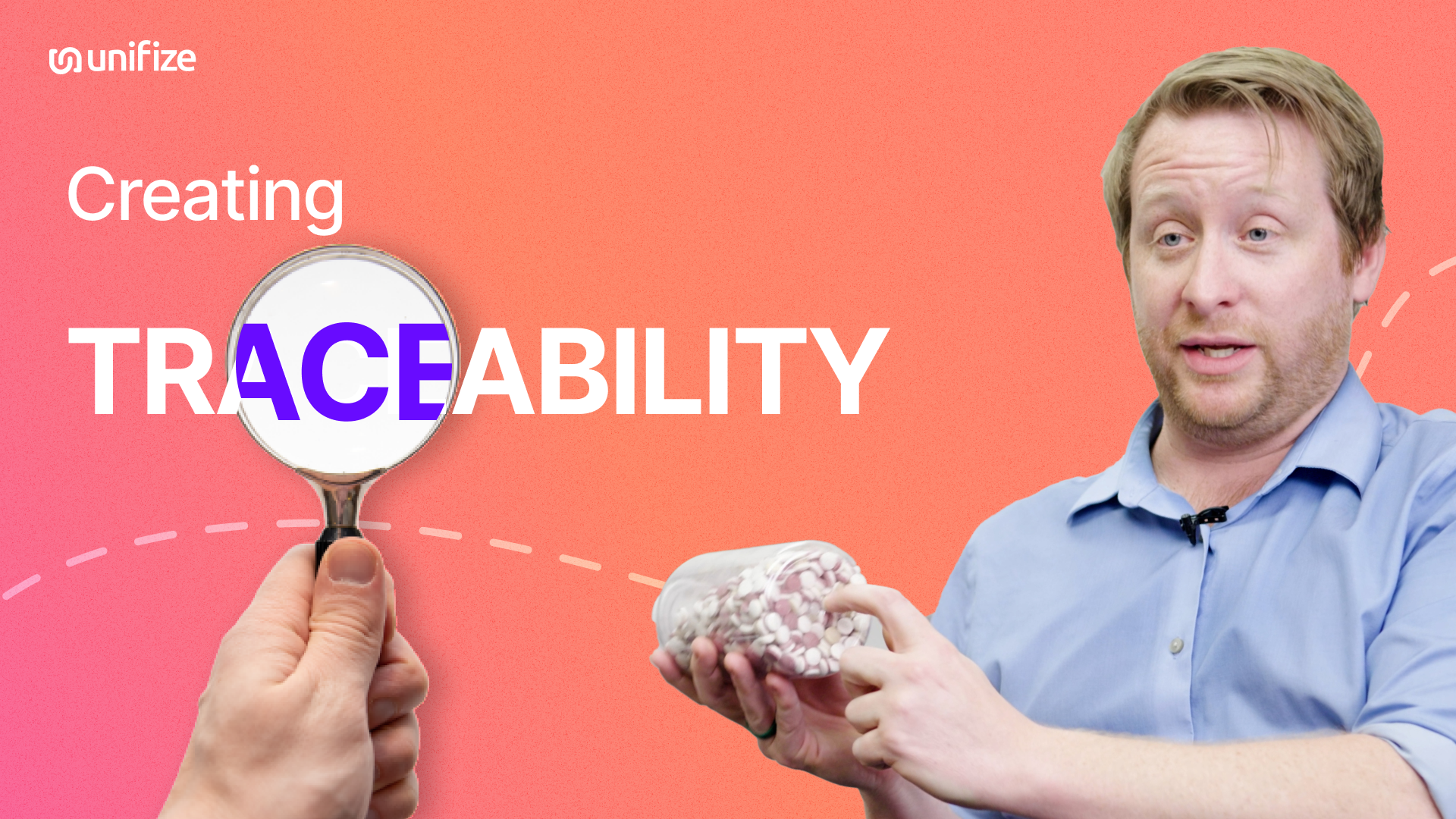

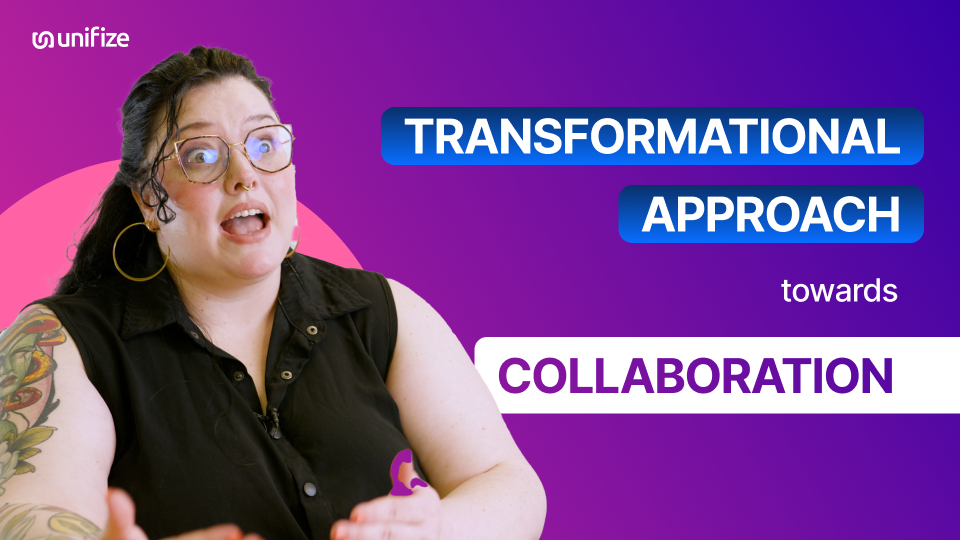

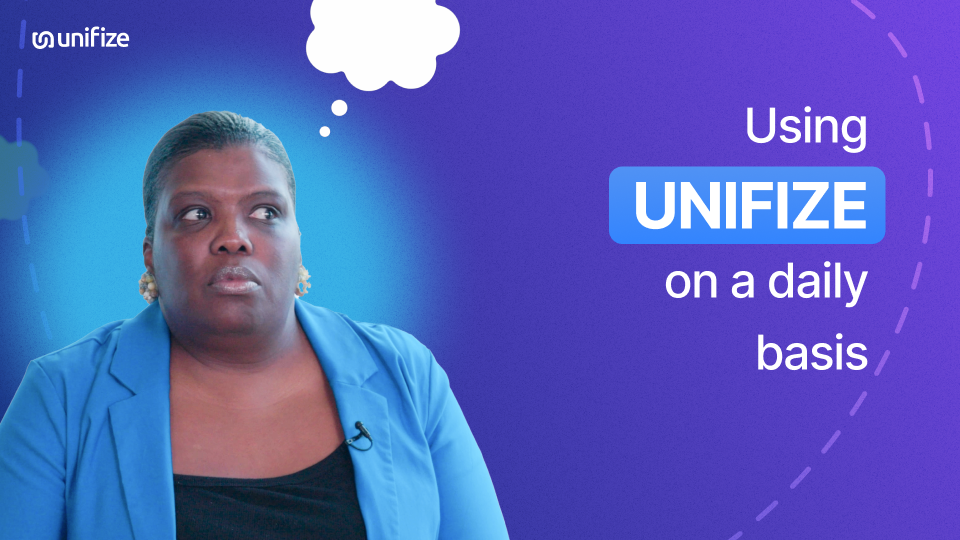

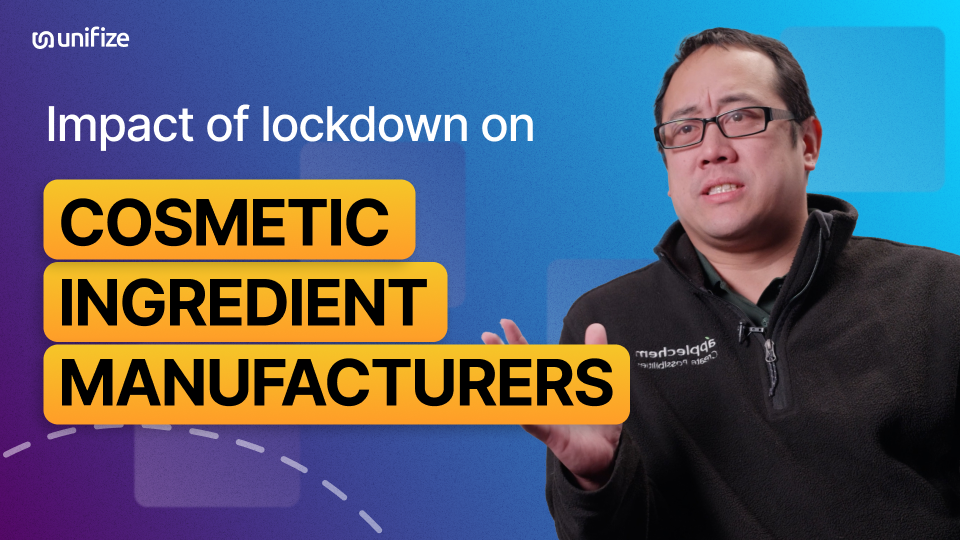

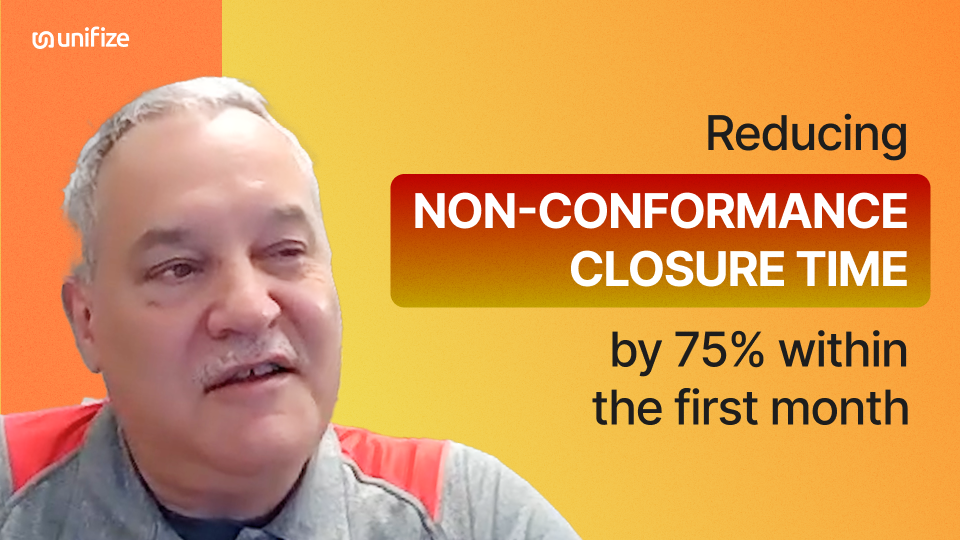

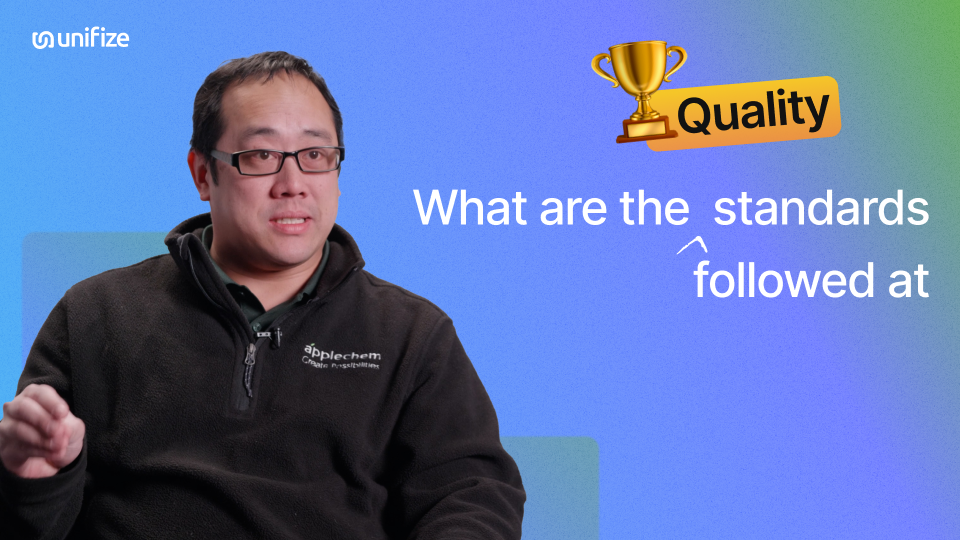

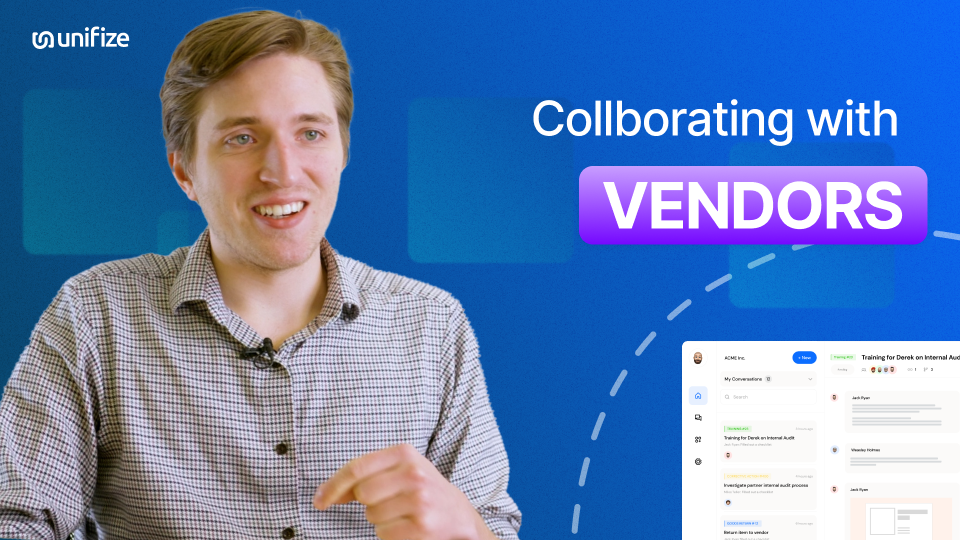

Experience the benefits of Unifize
4x Faster time-to-market
Map Unifize to your processes and streamline workflows, process automation, and prioritization
70% Fewer meetings
Less meetings with in-app collaboration, real-time updates, and decision logs
10x Speed to compliance
Unifize accelerates compliance, delivering 10x faster regulatory approval for medical devices