Content Library
[00:00 - 00:06]
As a senior quality engineer and in general, one of the most important things for quality is risk management, especially in the medical device space.
[00:07 - 00:14]
So you really have to focus on, how can this product go wrong and how we're going to make sure that it's safe for the patient.
[00:14 - 00:21]
You know, and that's the most important thing. You can have these innovators and create these beautiful, wonderful devices.
[00:21 - 00:45]
If there's an error or if something happens with it and you have somebody, you know, God forbid, die or something terrible happened to them, you know, you really need to think about how we're going to protect the patient because that's why we all got into medical device, right? You want to make the world better for people. You want to make things that are going to make people's lives better. And one of the ways to do that is through risk management.
[00:50 - 01:31]
Very basic level, you have a device and you look at every specification you have your user needs, right? Why did you make the device the way it is? You know, how is this going to help the user, How is it going to help the patient? And you take those user needs and you break them down into requirements and further into specifications the best way that I have to explain that is, for example, you know, yes, you want something to be able to be easily disconnected, right? There's lots of ways of doing that. You could have something that screws down to hold it together and then you unscrewing it, removes it. But for example, in surgery, a surgeon doesn't want to do that.
[01:31 - 01:46]
You know, the product development side, you get to say, oh, how about a button? Or how about a switch, a clip on and off and, you know, it can be really easy to get overwhelmed by all these possibilities of solutions for a single requirement or a single user need.
[01:47 - 02:15]
And that's where risk measurements or risk controls can help you, Yeah, it might be great to have this button or switch or whatever, be able to solve this problem. But is that solution going to cause more problems how are you going to be able to control those risks down? I have the FMEA in my head, but you know, you have your user need, your requirement, your specification, which is usually something that you want to be able to measure.
[02:15 - 02:37]
And so then from there, you know, you look at your hazards, hazardous situations and your harms. So, you know, making sure that you're designing it right. If we're talking about DFM or design FMEA and so you say, okay, so we have this this saw blade slot, for example, it has to be a certain width and height.
[02:37 - 03:03]
What happens if you designed it wrong, If it's not the correct, You know what are ways can that affect the patient. So, in this example of surgery, you know, you might have difficulty being able to make the cuts you need to with those blades. You might have difficulty being able to get the exact angles you need. And okay, so now you have your hazardous situation, your hazard.
[03:03 - 03:12]
What about your harm? You know, what we really care about and what the FDA and these other regulatory bodies care about is how that affects the patient.
[03:12 - 03:41]
If you're not able to do what you need to do, what are the issues with the patient? Is it going to be a delay in treatment? Is it going to be pain or they're going to have issues with their quality of life in the future? all of the different harms that could happen to a person because of this one feature right. And so once you have that, you also need to connect to, you know, you're required by law to control all of those risks down to as far as possible.
[03:41 - 03:47]
You know, you need to do tolerance stacks, any kind of verification and validation.
[03:47 - 04:14]
So you have to have various types of tests, you know, where tests, user validation, other verification activities to make sure that what you've designed is correct. And based on that, you can make an educated decision in order to bring your occurrence level down. I forgot to mention risk, you know, on the basis part is defined as occurrence times severity, and that's how you get your risk number.
[04:14 - 04:27]
And so, for example, one of your harms might be a mild annoyance to the patient, but if it's going to happen every time, then you really need to figure out a way to control that down and reduce the risk.
[04:27 - 04:37]
That's primarily kind of the basis of risk control is trying to reduce the occurrence by doing all of your due diligence to be able to make something that's safe and effective for the patient.
[04:37 - 04:50]
So through using Unifize, we are able to define our risk, our risk definitions and maintain all of our documentation and our specifications there.
[04:50 - 05:31]
And so in some places you can store your risk documentation and your risk analysis. You know, as a document process and keep that separate. But if you want to go further, you know, you can make your own input output matrix matrices through Unifize. You know, you can have a process where you define each of these design choices and specifications, connect them to your user needs, and then you're able to show the outputs of those, you know, which is really important to be able to see, you know, what's the problem you're trying to fix the user need and your requirement and how you are creating what you are creating to fix that.
[05:31 - 05:33]
And so you're able to track that in Unifize,
Risk Management made easier on Unifize

Customers
Denis's experience with Unifize: Revolutionizing quality assurance systems
Quality expert Denis details his transformative journey with Unifize. He praises its efficient design, user-centric approach, and the system's ability to streamline data handling and accelerate time to market.
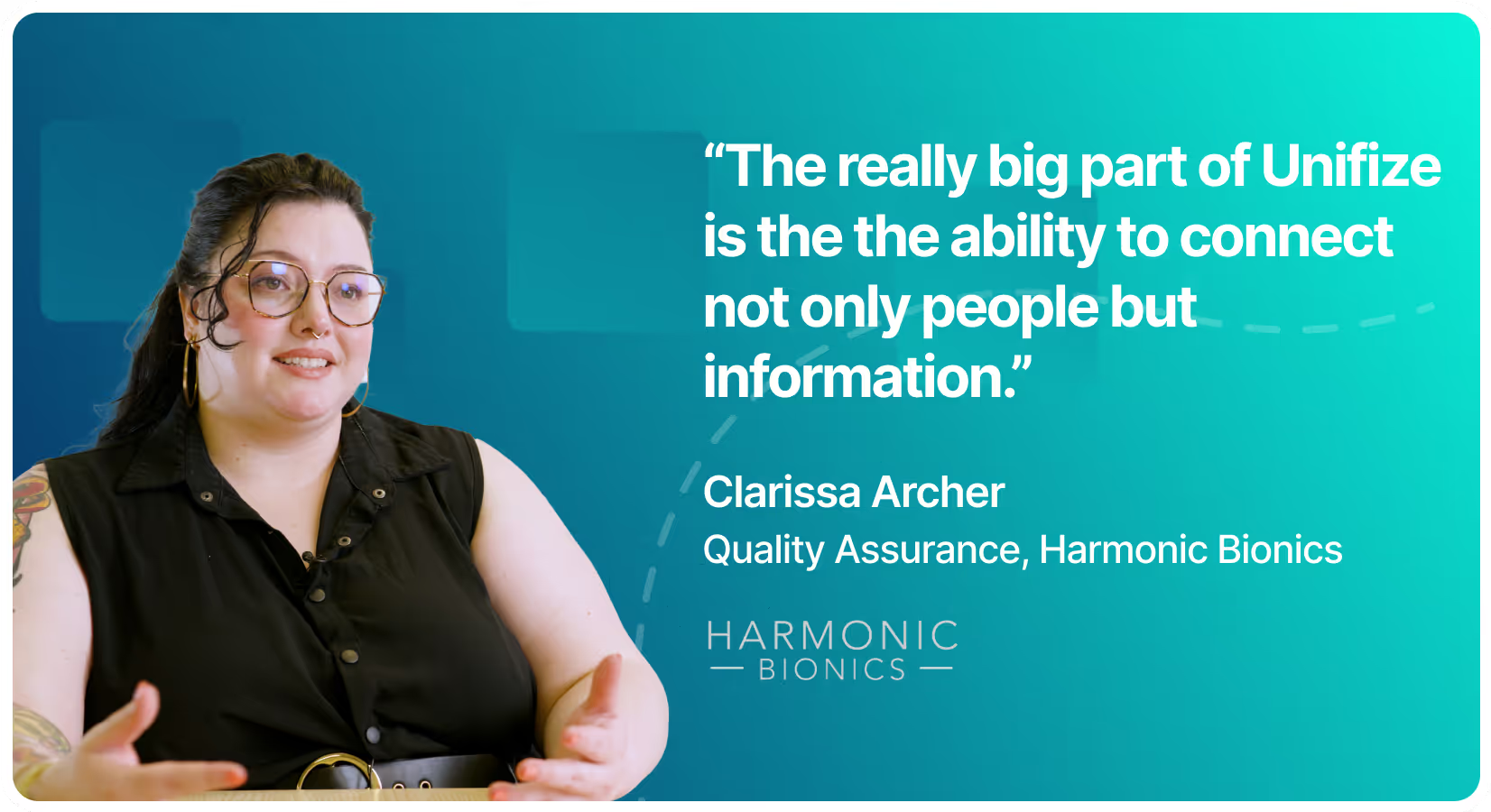
Customers
Harmonic Bionics and Unifize: A seamless transition to regulatory compliance
Clarissa Archer shares her experience integrating Unifize into Harmonic Bionics, underscoring its value in streamlining change control, facilitating communication, and ensuring robust documentation for regulatory compliance in the medical device sector.
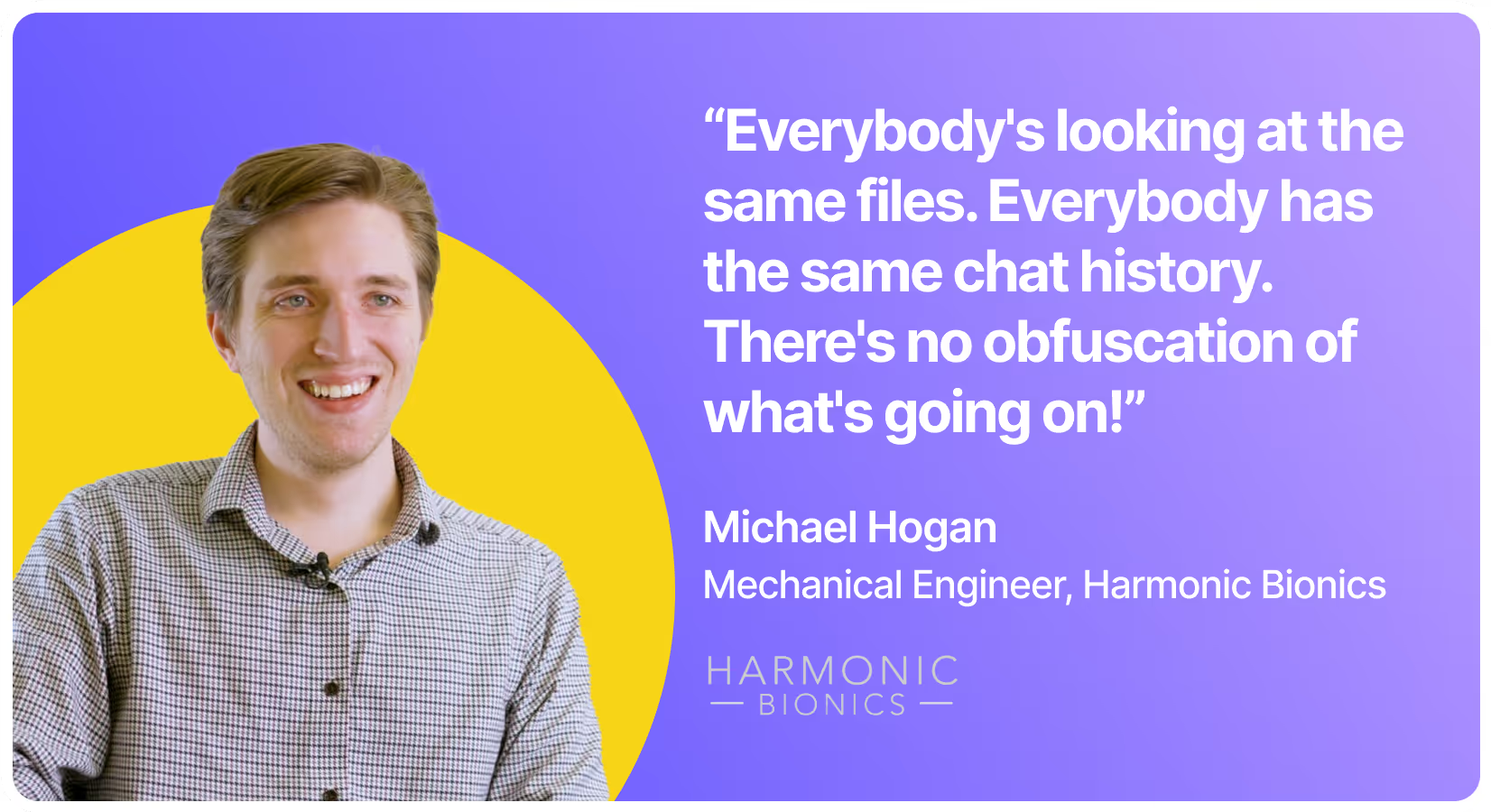
Customers
Engineering efficiency with Unifize: Michael Hogan's insights from Harmonic Bionics
Mechanical Engineer Michael Hogan elaborates on how the integration of Unifize at Harmonic Bionics has streamlined his engineering processes, promoting transparency and rapid turnaround in the medical device domain.
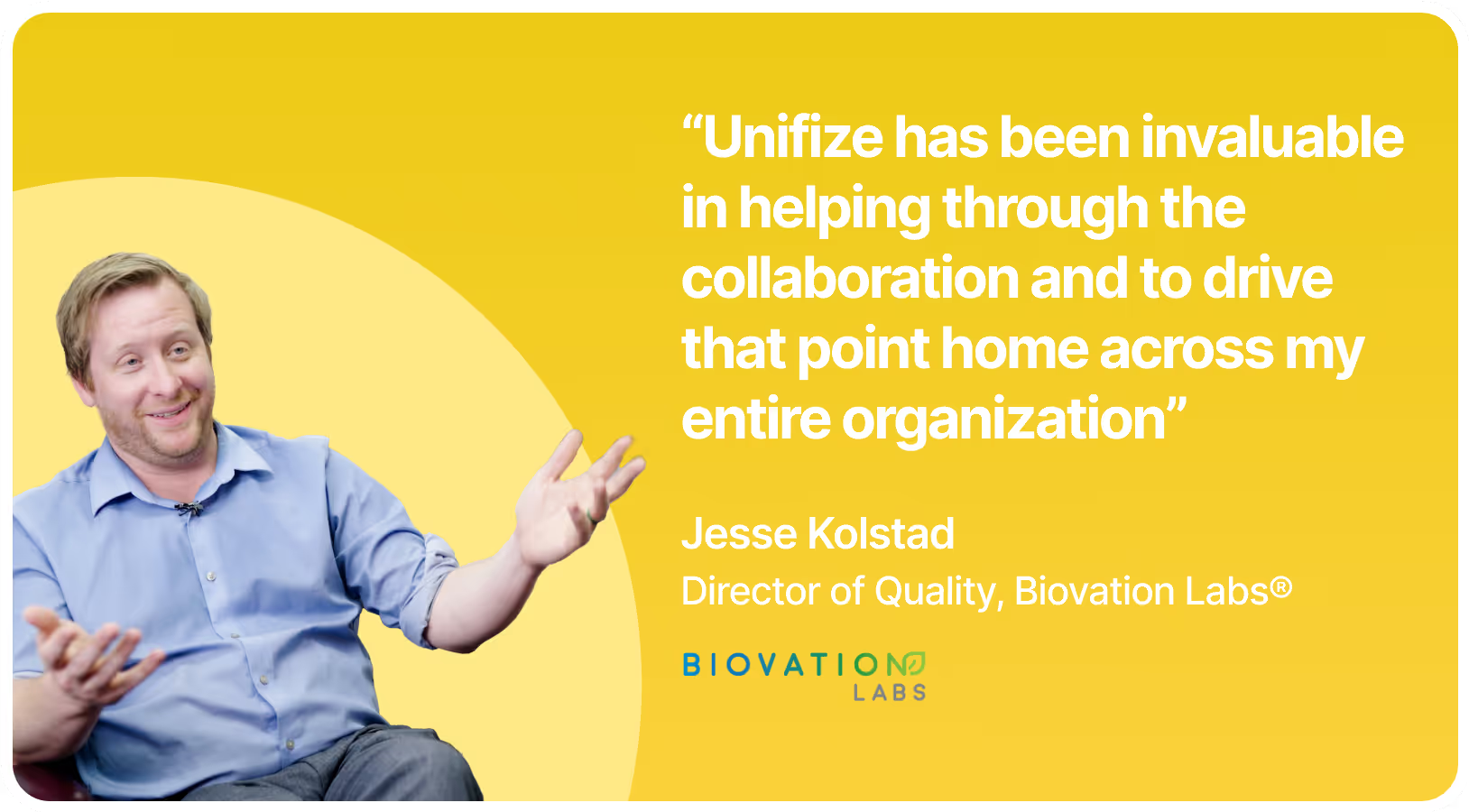
Customers
Here’s how Biovation Labs reduced testing costs from $146K to $65K in two months
Learn how and why Biovation Labs, an FDA regulated nutraceutical manufacturer based in Salt Lake City, took the decision to transition from MasterControl to Unifize for their product lifecycle (PLM) and quality management (QMS) processes.
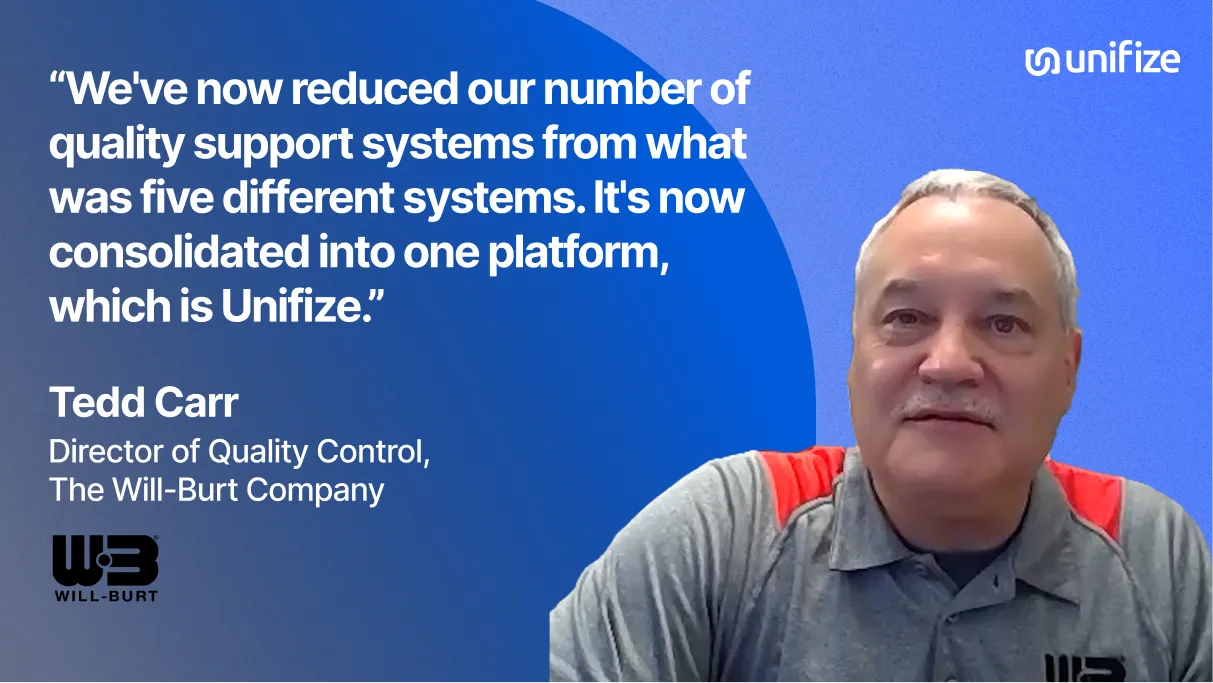
Customers
How a quality veteran from boosted issue closure time by 75% within the first month
Tedd Carr from The Will-Burt Company discusses overcoming their diverse and complex quality challenges across various sectors with Unifize. By consolidating five systems into one, they achieved clear accountability and reduced issue closure from months to days, demonstrating significant efficiency gains and faster decision-making in their quality processes.