Michael Hogan, a mechanical engineer at Harmonic Bionics, specializes in optimizing the company's groundbreaking rehab robotics. With a focus on tangible results, he seamlessly integrates quality management systems, ensuring rapid, efficient design iterations for the transformative Harmony SHR.
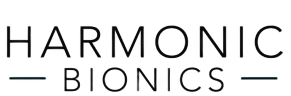
Introduction
Harmonic Bionics, a pioneering medical device startup, has revolutionized its engineering processes with the integration of Unifize. This case study delves into the experiences of Michael Hogan, a mechanical engineer at the company, highlighting the substantial improvements in workflow, communication, and documentation since the implementation of Unifize.
Challenge
Before Unifize, the engineering team at Harmonic Bionics faced delays and a lack of communication in their quality management system. Designs seemed to be thrown “over the fence” with little to no feedback, leading to a black hole of information. This lack of transparency and delayed responses were not conducive to the fast-paced environment of a medical device startup where time is of the essence.
Solution
Unifize was introduced to address these inefficiencies. A platform designed for real-time collaboration and documentation, it quickly became the central hub for all engineering outputs. Michael Hogan's day-to-day activities, ranging from creating PowerPoint presentations for design reviews to managing supplier information, were streamlined as Unifize served as the single source of truth for all product-related data.
Real-Time Collaboration
With Unifize, the entire team could see the progress of designs and documentation in real-time. The common chat history and file access eliminated any obfuscation in communication, fostering a transparent environment where everyone was on the same page.
Documentation as a Record
The platform also functioned as a living record of engineering work, replacing the need for individual file systems. Whether it was about product information, risk management, or design requirements, Unifize provided a responsive and reliable source.
Accelerated Turnaround
The change order process, which once took weeks, was reduced to the possibility of being completed within the same day. This efficiency was not just a time-saver but also a game-changer in the competitive field of medical device innovation.
Results
The impact of Unifize at Harmonic Bionics was immediate and profound. Michael Hogan noted a significant reduction in turnaround time for closing out issues. What previously took weeks to get a response now could be initiated and approved within a day, ensuring that the company could move quickly from design to production, thereby accelerating the time-to-market for their flagship device, Harmony SHR—a bilateral upper extremity rehab exoskeleton aimed at revolutionizing stroke rehabilitation.
Efficient Utilization of Time
Michael estimates that 30 to 50% of his time is now spent interacting with Unifize, which sounds substantial, but it is indicative of the platform's role as a comprehensive tool for engineering outputs, thereby allowing him to focus more on his role as an engineer rather than on system management.
Conclusion
Unifize has not only simplified the documentation and quality management processes at Harmonic Bionics but also empowered the engineering team with the tools to perform their roles efficiently. Michael Hogan’s testimony stands as a testament to Unifize’s capability to transform the engineering process, making it more transparent, collaborative, and significantly faster, thus aligning perfectly with the dynamic needs of a medical device startup.
As an engineer, right, my job is to solve problems with the product and make sure that we have a good saleable device that hits the market and does what it needs to it. That helps people. And if I do that, if I do my job as the engineer,
[00:14 - 00:30]
The way that we've set up our QMS with Unifize I'm just writing what I've done and that's the process, right? It is a time saver for me because ultimately I need to think about the system less and I can just focus on my job more,
[00:34 - 00:51]
Hi, my name is Michael Hogan, I'm a mechanical engineer here at Harmonic Bionics, and I deal with the nuts and bolts of Harmony. We are a medical device startup and we're working to bring rehab robotics into the upper body stroke rehabilitation space.
[00:51 - 01:04]
Our flagship device is Harmony SHR. It's bilateral upper extremity rehab exoskeleton. So my day to day work here at Harmonic Bionics, I primarily interact with our change order process.
[01:04 - 01:13]
I interact with our deviation, non conformances, and quality notification processes for material that comes in and has issues, that sort of thing.
[01:13 - 01:28]
For my workflow in my day to day work, I probably spend about 30 to 50% of my time interacting with Unifize in some way. That sounds high, but that's because we use it as a document of record for engineering outputs.
[01:28 - 01:48]
You know, I might be making a PowerPoint presentation for a design review that's intended to live in Unifize, right? That that's part of that 30% of that time. Or I might be looking at supplier information that is stored in Unifize. It is the easiest source of record for things that I need to find to do my job.
[01:48 - 02:07]
Some people maintain a nice file system on their computer of all their engineering work. Our Unifize system is kind of set up in that way or most everything I need if it's information about our product or about our risk management file or about our design requirements, I go to Unifize to get that. That's where I go.
[02:07 - 02:14]
It is very responsive. And if I need to get something done now, it gets done now. I can cut to the chaff and get with them what needs to get done.
[02:18 - 02:33]
The relationship I've had with a quality management system in my previous roles has more or less been: Get your design together, throw it over the fence, and two or three weeks later you might get an email saying that you need to add some field to a part property or something like that.
[02:33 - 02:51]
There's no communication back and forth. As far as I knew, it was just sending parts out into the void. With a smaller company, you cannot do that, right? There's nobody in the void to send it to. And more importantly like that, those two weeks you don't have. We need to get this stuff out now.
[02:51 - 03:00]
And So what I like about Unifize is that I see exactly what's happening with the information or the designs that I am putting forward to get released.
[03:00 - 03:16]
Everybody's looking at the same files. Everybody has the same chat history. There's no obfuscation of what's going on. Having a common understanding of the process that our parts designs, our deviations, quality notifications are going through is really useful.
[03:16 - 03:28]
I mean if you think about in just raw turnaround time to close out an issue. In the past, you know, a design update where I'd get all my paperwork ready, send it off, wait two weeks to maybe get a response.
[03:28 - 03:34]
Now, like literally after this meeting, I may go out and submit a Change Order and it will be approved, maybe even by the time you guys leave, Right?
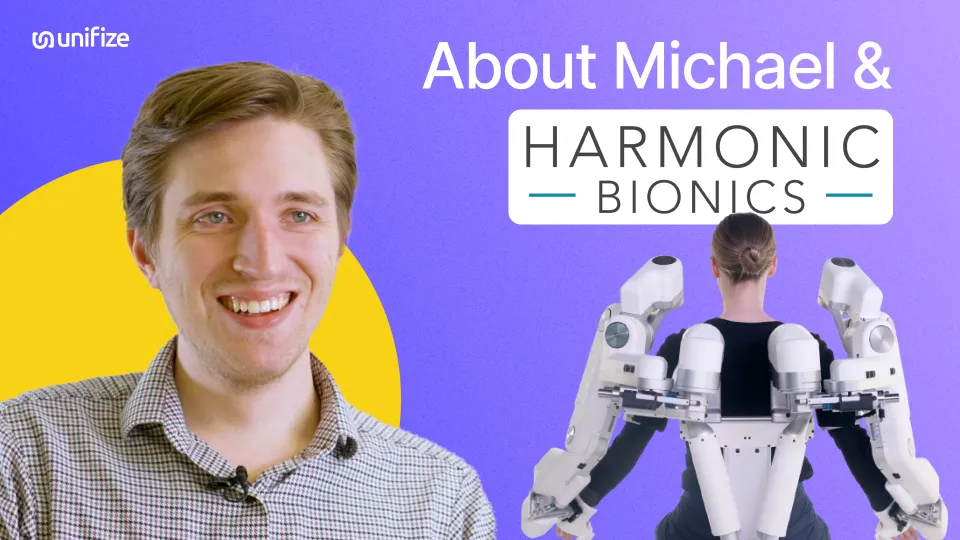

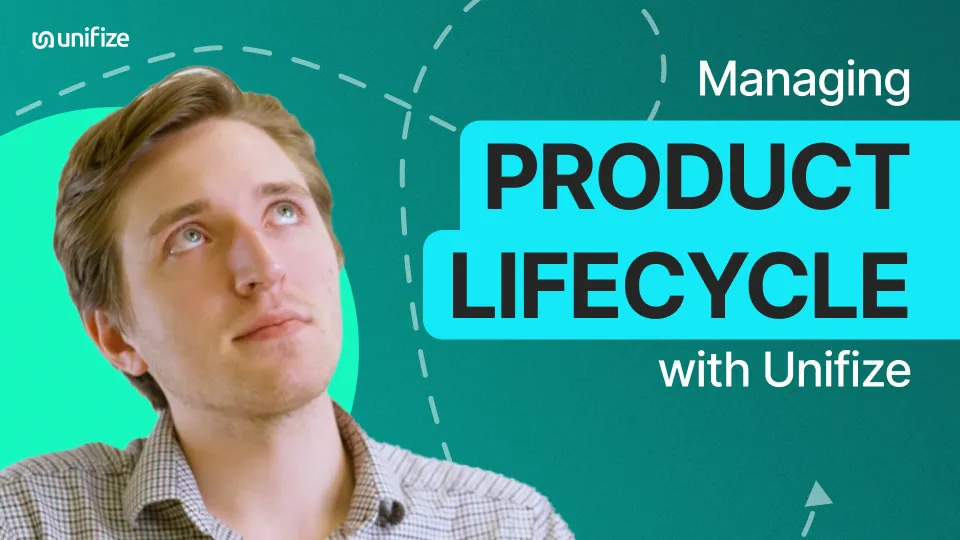

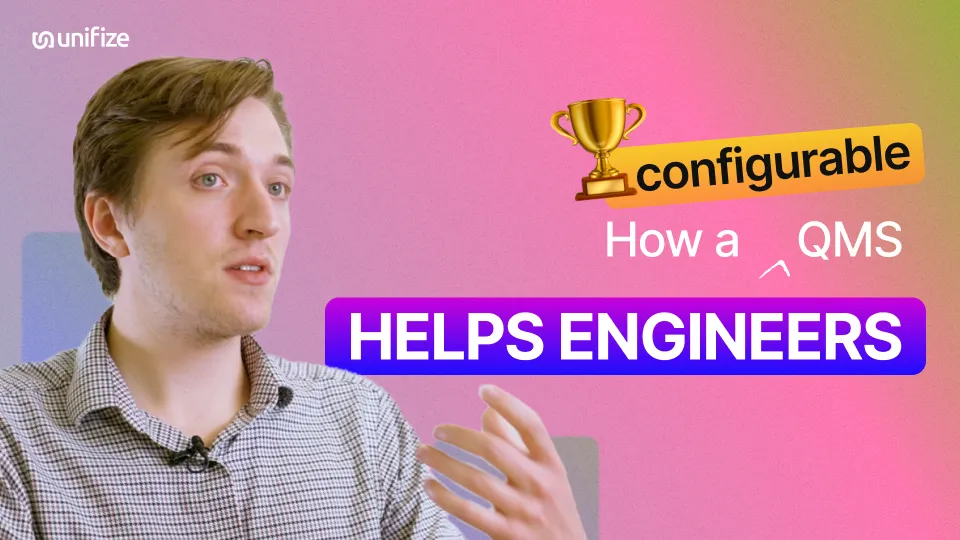

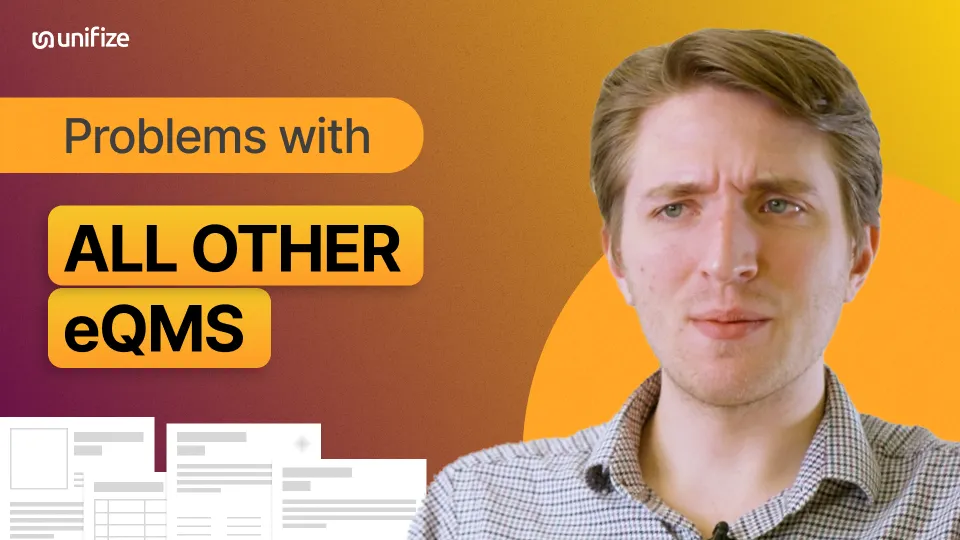

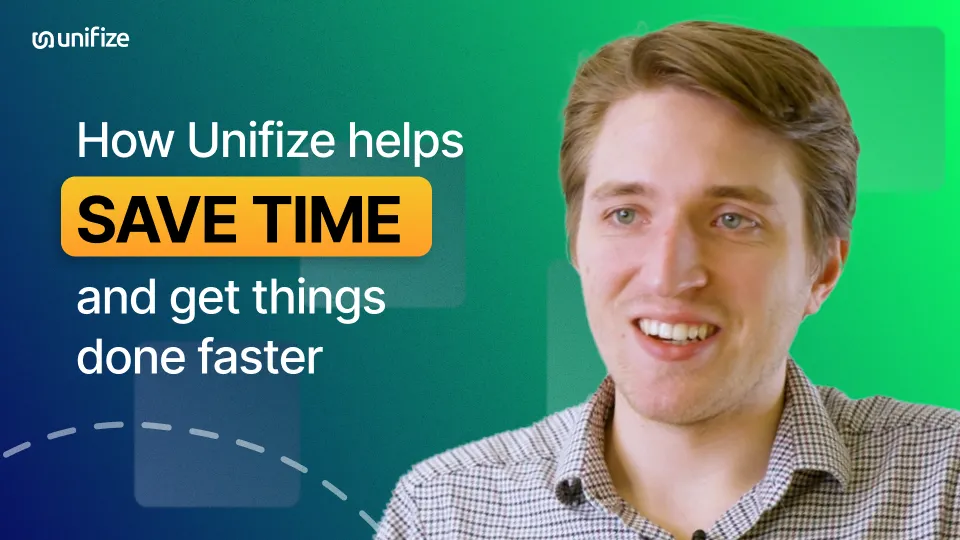

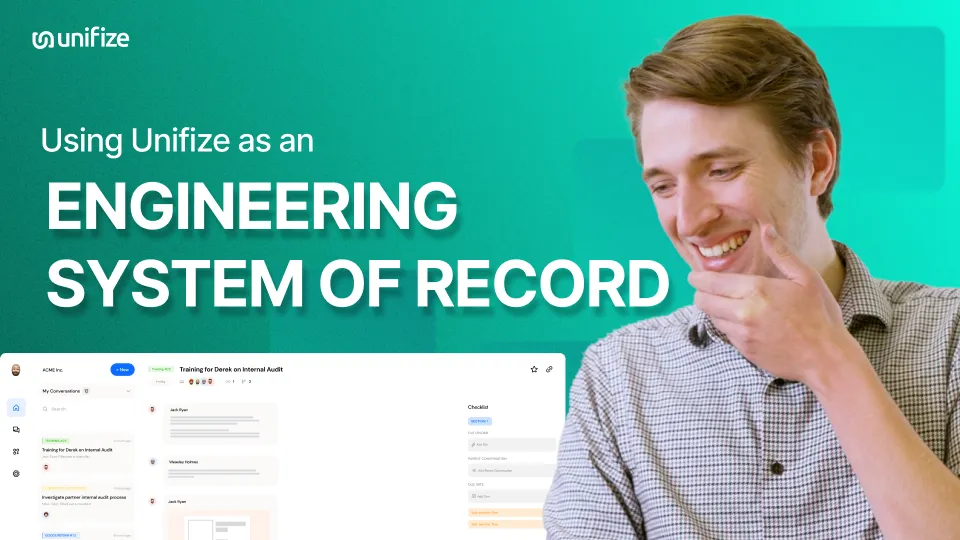

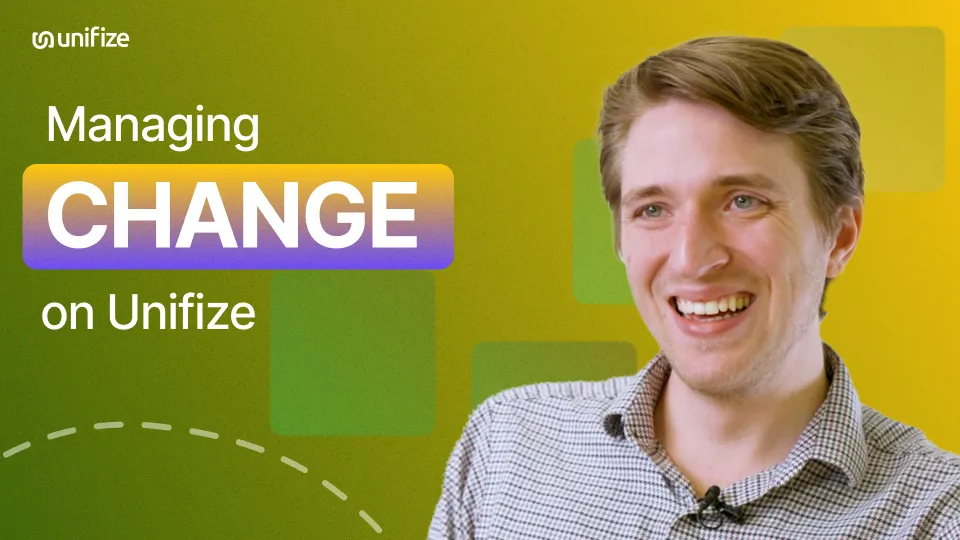

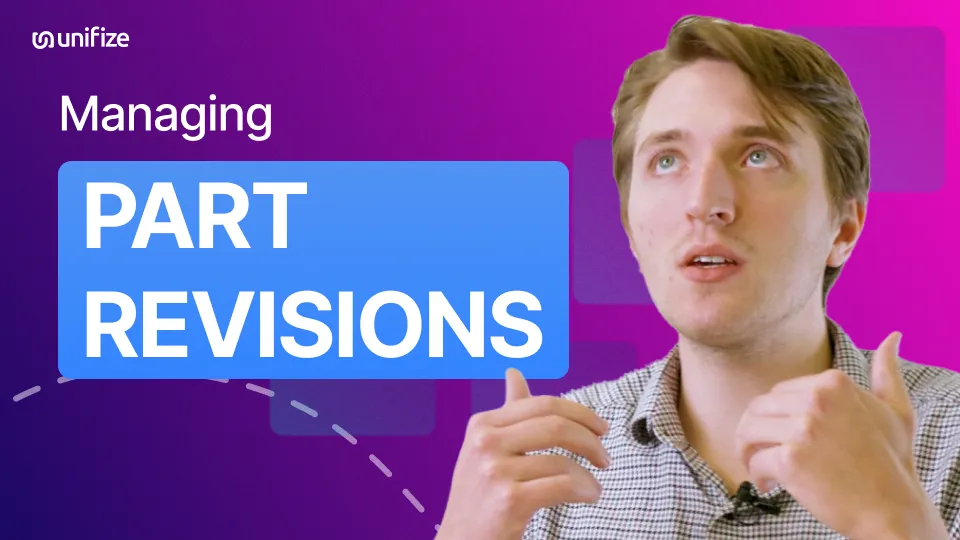

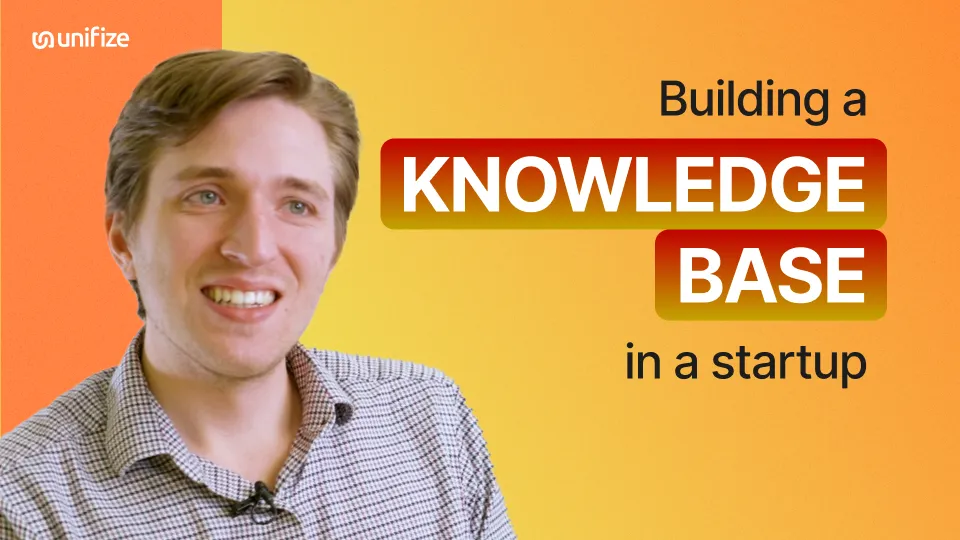

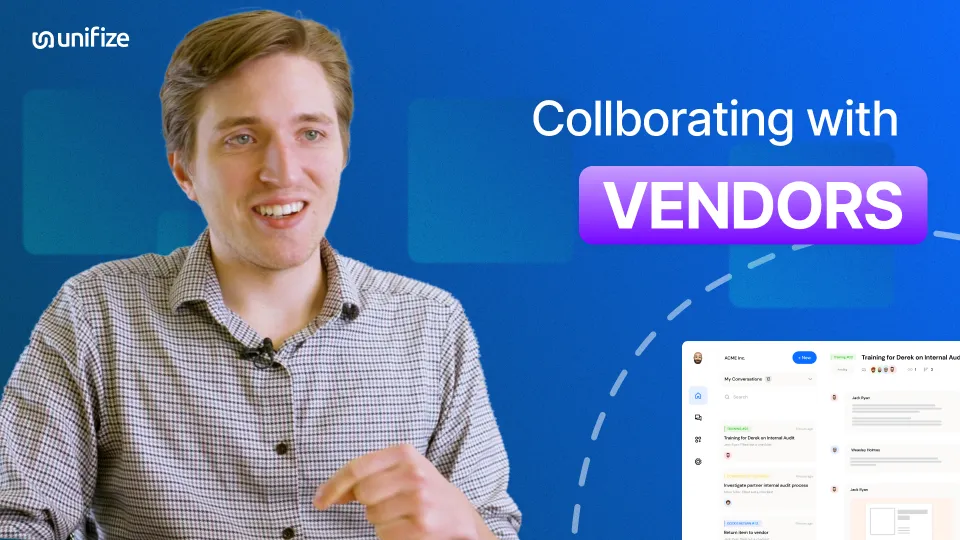

More from Michael Hogan
Unifize Results
Speed to compliance
Faster time-to-market
Fewer meetings